12. Kenoteq - K-BRIQ.
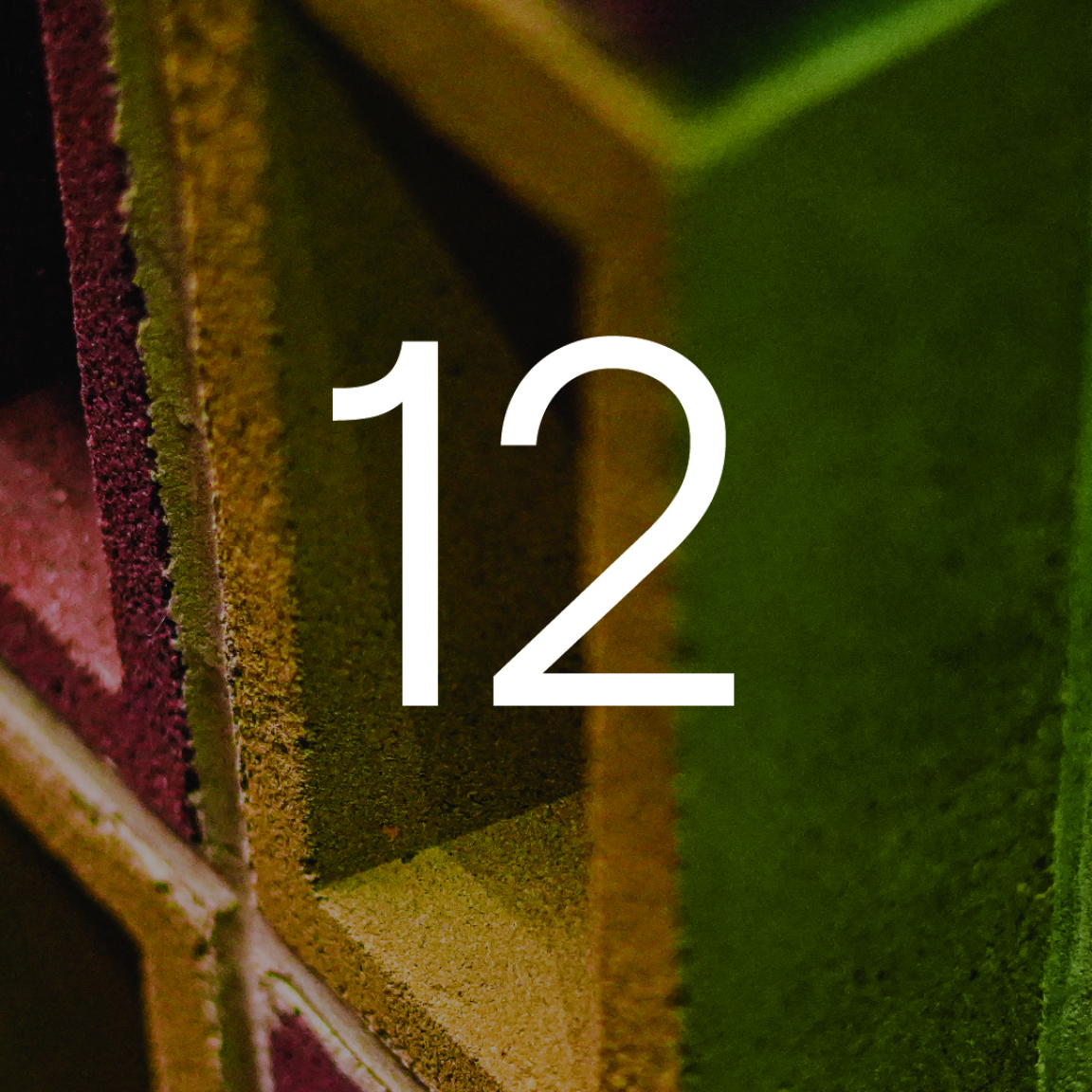
Kenoteq was established in 2019 as a spin-out from Heriot Watt University in Edinburgh on the back of nearly a decade of R&D into the circular, closed loop, ultra low carbon K-BRIQ.
The K-BRIQ is made from near 100% recycled waste. The majority of the waste is from certified inert recycled aggregates (rubble from old brick, old stone, and old mortars) together with recycled gypsum from waste plasterboard. "We also add recycled pigments to colour the product and a dash of our proprietary binder (our “secret sauce”!) to help bind the product."
Kenoteq works with two local waste management partners who collect, sort and process construction and demolition waste to strict protocols and provides it as certified inert processed waste streams to manufacture into the K-BRIQ and K-SLIPs at the company's cleantech factory outside Edinburgh.
A patented low energy production process uses hydraulic compression and is efficient, creates no waste and uses only 10% of the energy of traditional brick production. The whole production process takes only 24 hours, significantly quicker than traditional brick production. Importantly it does not fire the products, allowing for an enormous energy saving and reduction in carbon emissions.
Designer: Kenoteq
Project: K-BRIQ
Material Breakdown: Near 100% recycled construction and demolition waste (rubble from old brick, stone, and mortars), recycled gypsum from waste plasterboard, recycled pigment, and binder
Main Uses: Built environment – internal and external
Key Fact: The K-BRIQ has recently completed its final certification testing with the British Board of Agrement (BBA) with final certification expected by the end of 2023.
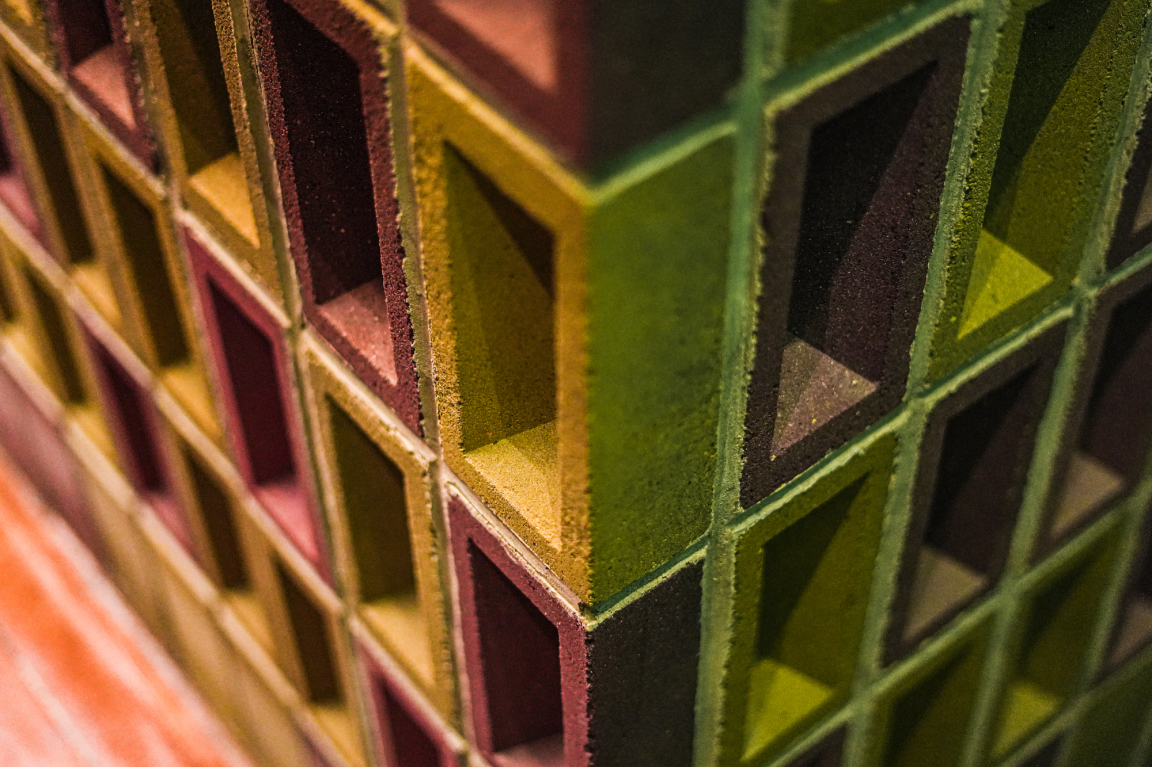