First 3D printing filaments made from post-consumer single use plastic waste.
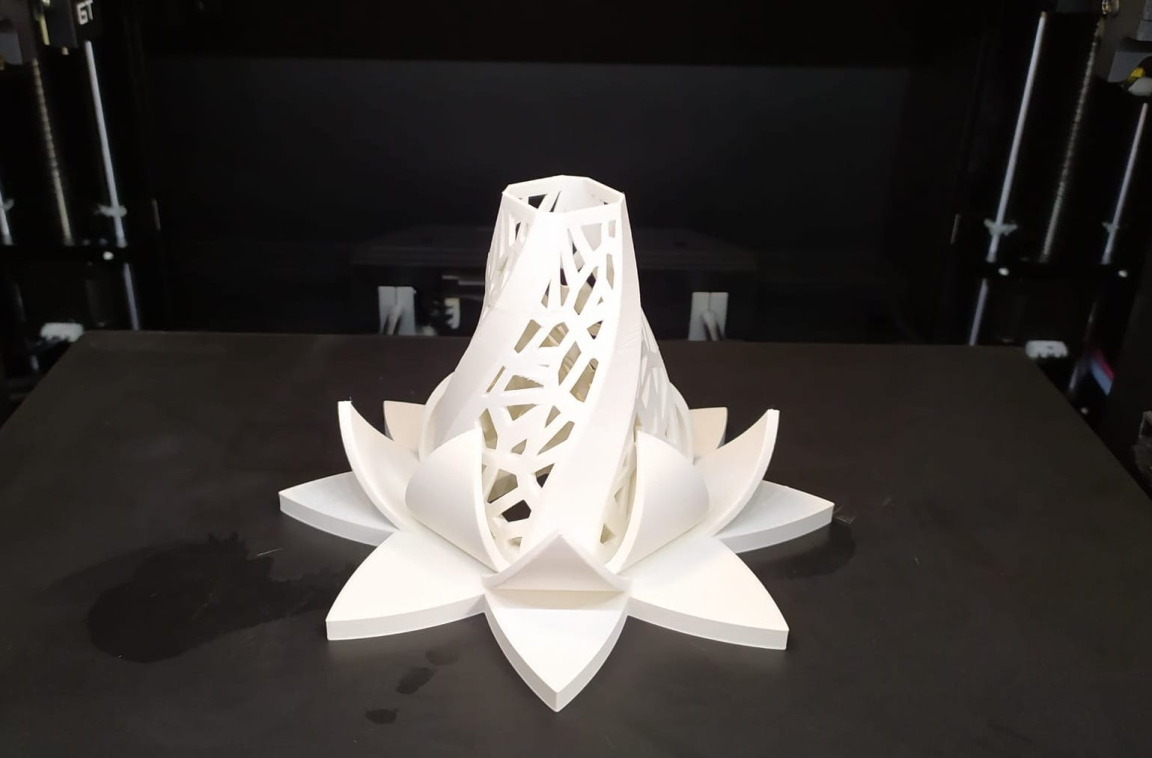
As part of an international research project, led by Manchester Metropolitan University, post-consumer, single-use plastic (SUP) waste has been successfully transformed into 3D printing filaments – which will eventually be used by businesses to make sustainable new products.
Researchers from the University have developed the new filaments using recycled, post-consumer, SUP wastes, including materials commonly found in plastic drinks bottles and coffee cup lids.
As a result, thousands of tonnes of waste – which would otherwise have ended up in landfill – will now have the opportunity to be made into new, higher value products.
The development of the new filament marks a milestone in the TRANSFORM-CE project, funded by Interreg North West Europe.
TRANSFORM-CE aims to drive the uptake of single-use plastic materials by businesses across North West Europe, using additive manufacturing and intrusion-extrusion moulding to turn these valuable resources into new products that can be returned to the process a number of times.
Whilst other recycled 3D printing filaments exist, TRANSFORM-CE will take the process to the next level developing 3D printing filaments at a larger scale and creating wider uptake than has been seen previously.
To do this, researchers have been carrying out extensive testing on the recycled SUP – which can be difficult to print with – to formulate a consistent and reliable filament with quality print results, so that it can be easily used by businesses.
As part of the project, small and medium sized enterprises (SMEs) will be able trial the filaments helping them to experience the benefits that 3D printing technology can bring to their business, whilst incorporating recycled post-consumer plastic waste for the first time.
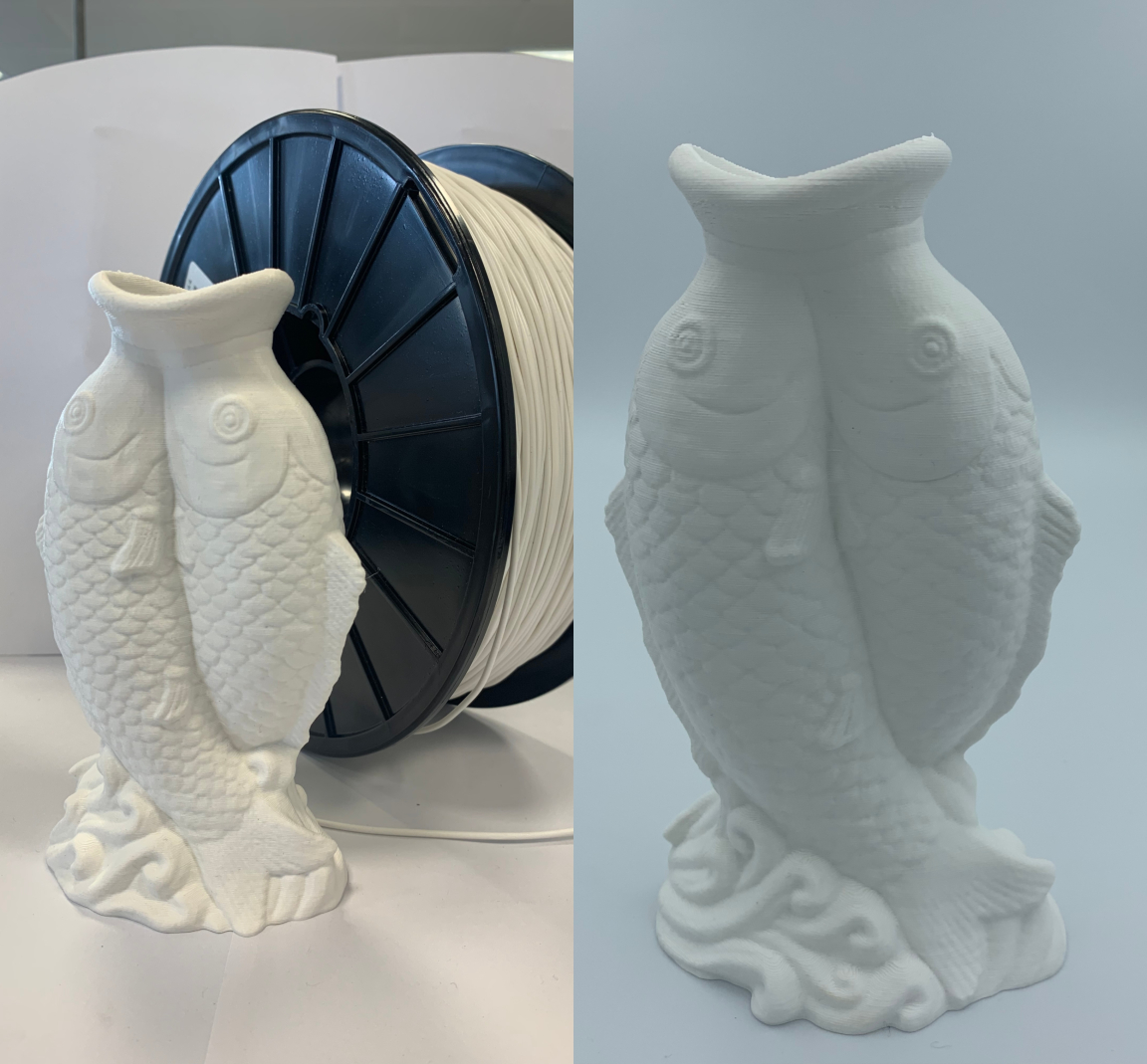
Craig Banks, Project Investigator and Professor at Manchester Met said: “A common problem with creating recycled 3D printing filaments from post-consumer single use plastic waste is the fact that these materials can be challenging to print.
“This is something that TRANSFORM-CE is addressing through the development and application of unique formulas and additives that improve both the printability of the 3D printing filament and the quality of the finished print.
“This breakthrough will not only provide a new solution to the current single-use plastic waste problem, but also a new source of recycled materials for 3D printers.
“TRANSFORM-CE is a great example of circular economy in action, whereby wastes generated locally can be recycled and reused locally, creating material loops and generating value for communities and the local economy.
“The project is also establishing how many times these materials can be circulated in these loops, whilst still achieving a quality product.”
The successful development of the new filament signifies the launch of a new research and development centre at Manchester Metropolitan University, which will house the technical equipment used for filament production and experimentation, alongside 3D printers for testing the filaments.
A demonstration centre will be home to some smaller-scale examples of the technologies used as part of TRANSFORM-CE, as well as showcasing product examples produced from the recycled single-use plastic materials and information about the project.
Samples of the filament will also be made available to businesses and stakeholders across the UK and to partners in Belgium, the Netherlands and Germany.
The latest milestone in the TRANSFORM CE project follows the opening of the Green Plastic Factory in the Netherlands earlier this year, which is the first intrusion-extrusion moulding plastic waste recycling plant of its kind in the country and aims to support the transformation of SUP waste, collected from the local waste stream, into new products.