Newhey Carpets on why specifying sustainably is crucial.
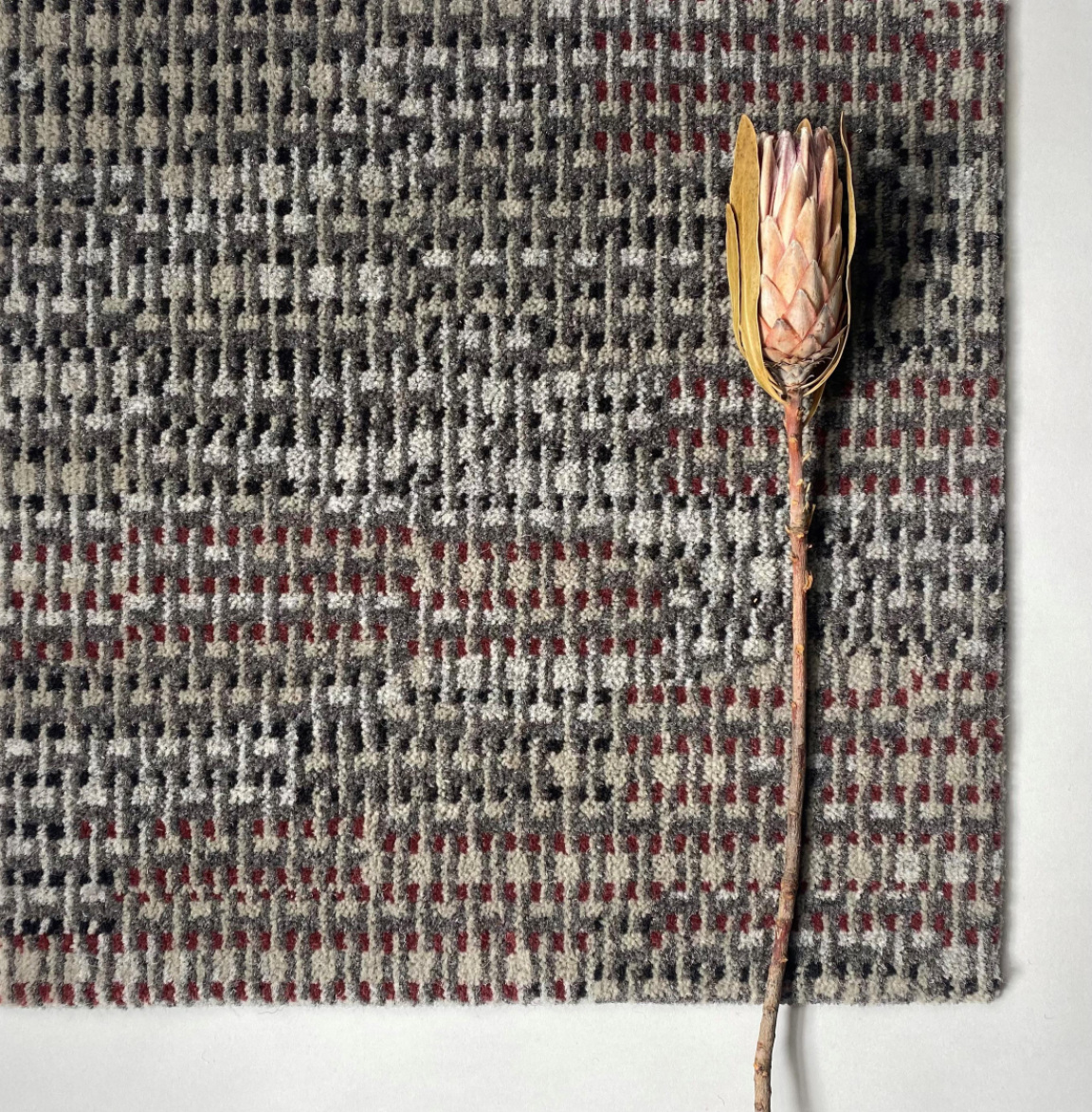
The impact of climate change is global. It’s already having a visible effect on the world, such as changing weather patterns which threatens food production, to rising sea levels and catastrophic flooding.
At the COP26 conference in Glasgow, world leaders made some huge decisions about how their countries would help lower their carbon footprint in order to help reduce greenhouse gas emissions. David Attenborough’s Netflix show also highlighted the fact that every single one of us needs to be more mindful of our actions if we’re going to save the planet from the inevitable. It is more apparent than ever that embracing these environmental initiatives can no longer be ignored but by working together we can tackle these challenges.
The growing pressure within our industry makes it imperative that we exceed customer requirements and produce products in a more environmentally responsible way.
Sustainable manufacturing for the hospitality and leisure sector is essential, therefore, our environmental priorities are to reduce carbon emissions, water consumption and waste.
Taking sustainable steps
So the question is, what steps have we made so far to be an environmentally responsible manufacturer and how are we going get to net zero in the future? Reducing energy consumption and waste, improving our manufacturing processes, choosing local suppliers and raising awareness with employees are among some of the points we’re going to talk about.
Being a family-owned and operated company, Newhey has always been mindful of ethical and sustainable production processes. In 1968, we began manufacturing carpet on traditional Axminster looms, however, over time, it was evident there were more efficient ways to do this. So, in 2002 we installed our first Colortec machine. The benefits of manufacturing carpet on high speed patterned tufting machines are immense. Not only is overall power usage and noise pollution hugely reduced, it’s also possible to produce twice as much in the same amount of time.
Making a good example and sample
Sampling has always been a busy department and producing bespoke hand trials used to be a timely process. We have progressed from producing sampling by hand to a new computerised method created by Modra Technology called Kibby. Producing an 18”x18” sample by hand would have taken around 5 hours, on the Kibby it takes an hour. Needless to say, this has numerous benefits such as improving productivity throughout the department and also reducing yarn wastage by switching to the computerised system.
We can back it up
Finding a more sustainable way of applying the secondary backing to the carpet was another milestone. In December 2008, we installed the world’s first 4-metre hot melt secondary backing line. Switching from a traditional latex secondary backing system to a solvent-free adhesive system – a high strength thermoplastic bonding agent which is essentially more sustainable.
Following this, the natural progression led us to explore how we could convert to a more sustainable backing material. In 2013, we sourced a brand new recycled secondary backing material called ‘evobac’, produced from post-consumer PET. Replacing the traditional ‘actionbac’ material, it recycles approximately 8 plastic bottles per square metre which, to date, has diverted at least 13 million plastic bottles from going to landfill or entering our oceans. The backing plant also uses less energy, less water and incorporates a computerised cutting table which minimises wastage.
Our building is a big part of our heritage. The main part of the factory was once upon a time, part of the Lancashire & Yorkshire Railway Cotton Warehouse, which brings us swiftly on to heating, lighting and insulation. Installing insulated roof panels as well as energy efficient motion sensor lighting and heating control systems throughout the factory has cut our heating costs significantly.
Supply chain
Localising our supply chain also represents a tremendous opportunity to help the environment. We’re proud to support our local economy by sourcing our yarn from local spinners and dyers based within a 35km radius of our factory. This reduces shipping and storage, and therefore cuts our emissions and energy usage.
New life for old off-cuts
Newhey is meticulous when it comes to planning and calculating how much material is required for each order to ensure overages and waste is kept to a minimum. It is essential, prior to going into production with any order, that quality, colour and design are checked by tufting a production sample. When the order is complete, this material is no longer needed. We send our carpet off-cuts and production waste to a textile waste merchant who specialises in recycling and shredding wool and other fibres. Waste carpet fibres are pulled and blended with other fibres and materials for use in underlay, sound and heat insulation products, helping to create a closed loop system instead of sending it to landfill.
Packaging
The world’s reliance on plastics is a major factor in the climate battle which is why it’s important for us to find the most environmentally responsible solution to wrap our carpets prior to despatch. It has been widely reported in the media that a new tax introduced by the UK Government will come into force in April 2022. Its aim is to try and raise the minimum level of recycled content in plastic packaging to 30%. All our carpets are already wrapped in product which contains at least 30% recycled content. It’s our aim to continually strive to source this material with a higher percentage of recycled content in the future.
Positivity from a pandemic
Like many businesses, coronavirus presented us with many challenges, however, throughout this period we were able to internally reassess our production processes. By streamlining these, we are working more productively and making efficiencies that will secure the long term viability of the company. We are also proud to employ a very local workforce and by being located directly next to the Metrolink, we can offer a convenient, environmentally friendly transport option for staff and visitors.
We’re proud of our sustainability journey so far. Whilst many points have been covered here, we are continuously pushing ourselves to find innovative ways to become even more environmentally responsible. Having already started the switch to hybrid cars for our staff, we’re also exploring the possibilities of installing solar panels and commercial rainwater harvesting.
The planet is our most precious resource and respecting it is one of our key company values. Solutions lie in constantly reassessing our production processes and applying a greener business model which we will continue to strive for going forward.