Top 24 3D print projects and practitioners for 2024.
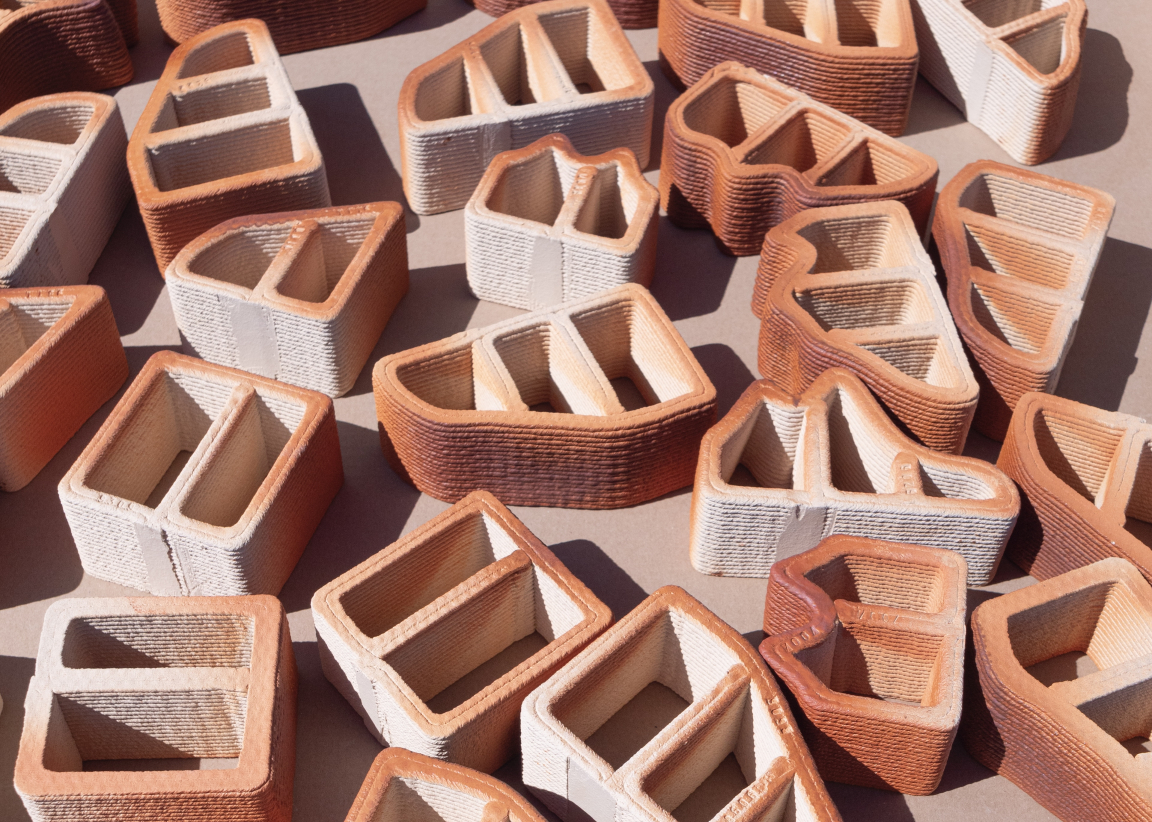
Studio RAP: Ceramic house bricks.
3D printing is revolutionising the construction industry - we believe, for the better. Whether it be fusing hand-making with technological advancements, generating new concepts for the built environment, or creating circular systems over linear - it’s an industry to watch intently.
Though the technology itself isn’t a new concept, having informed product design prototyping and architectural model making for several decades now, the scope for using these digital technologies is widening, and at pace.
Looking specifically at our sector, Material Source Studio Manchester partner, Gresham, has been using this technology since 2016 to help progress from initial concept to product with both speed and confidence. Now working with the team at PrintCity in Manchester, product designer at Gresham, Steve Parkinson shares with us that it is now embracing 3D scanning and VR visualisation techniques to develop its product offerings.
Following on from our list of 24 bio and by-product based materials for 2024, and hot on the heels of our Full Circle Concrete exhibition in Manchester, we are continuing to celebrate the breadth of outcomes and circular material solutions aided by technology.
Here we share some of the innovations taking place across the globe - a number of which are hatching on our doorsteps in both Manchester, and Glasgow. Through splitting this design directory on additive manufacturing into three categories; Build, Filament and Surface - we’re pleased to put forward an eclectic portfolio of impressive 3D printed architectural builds, recycled and regenerative printed materials, and limitless surface qualities.
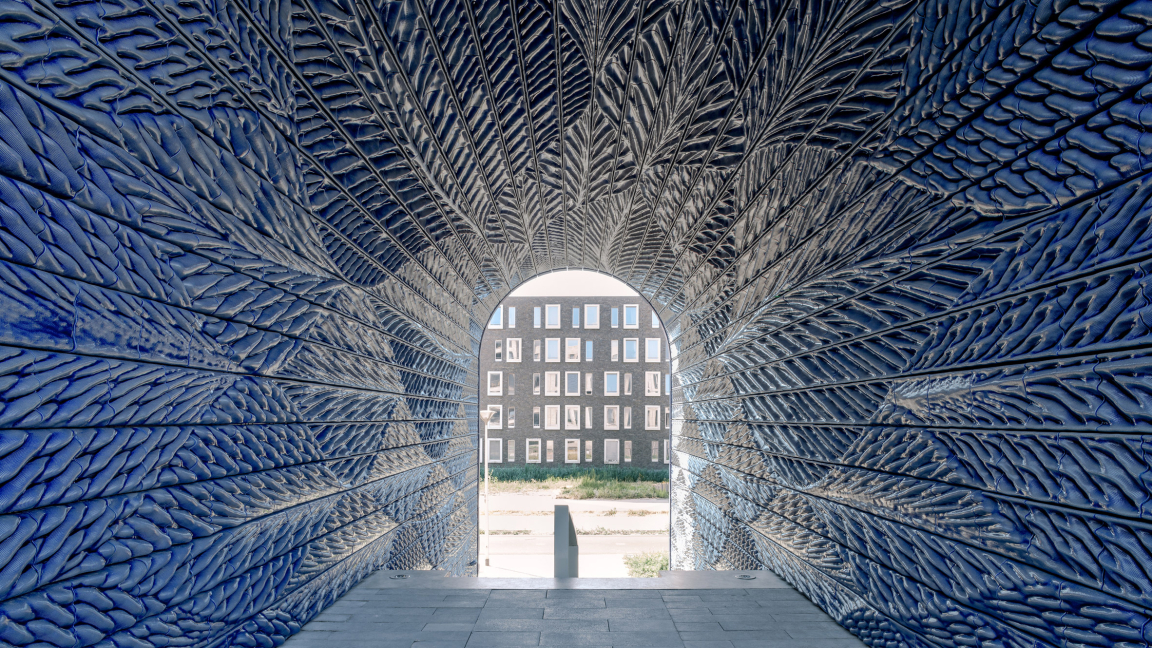
Studio RAP: New Delft Blue Archway.
Build
From minimising human labour, cost and project timelines, to manufacturing geometries which would be deemed impossible using conventional construction methods, 3D printing puts forward numerous pros to improving efficiency within the construction industry.
1. Studio RAP - The New Delft Blue Archway
Studio RAP is an architectural design company on a mission to innovate the way it designs, builds and manages architecture. Together with robots, its team of architects, designers, robot engineers, programmers and researchers harness the power of computational design and digital fabrication to produce architectural façade cladding and building concepts to a global collection of clientele.
Through a symbiosis of large-scale printing technology, algorithmic design and artisanal glazing, Studio RAP delivers truly outstanding, liquid-like, ceramic structures that are sensory-rich, changing the surface qualities of the built environment as we know it.
One of its most recently completed pioneering projects, New Delft Blue, is a historic nod to the Dutch city of Delft. The glistening, blue tunnelway is a re-interpretation of the renowned decorative qualities and design vocabulary of Delft Blue porcelain. Using cutting-edge technological advancements, New Delft Blue gives new insight to the architectural potential of ceramic ornamentation for the 21st Century.
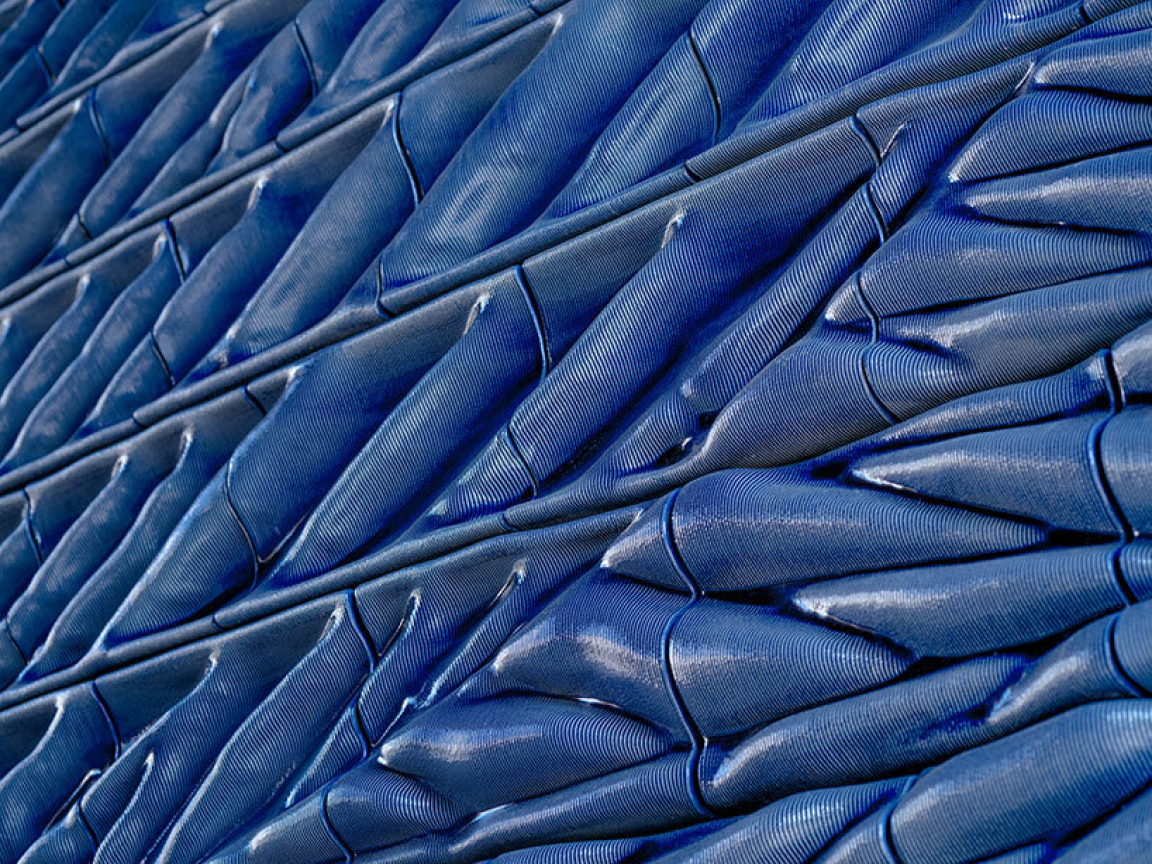
Studio RAP: New Delft Blue Archway.
2. Hassell X Nagami – A 3D printed public pavilion
International architecture studio Hassell has joined forces with the creative collective and 3D printing studio, Nagami in order to develop a 3D printed public pavilion, all made from recycled plastic.
Taking inspiration from indigenous shelters, the prototype aims to serve as a gathering spot for reflection and education, whilst being easily customisable to withstand a wide range of extreme climates and settings. Viewing the billions of metric tonnes of plastic waste produced by the planet as a resource, the design team aim to re-divert this monumental waste stream into full scale, functional architecture.
With the prototypes developed and undergoing testing, it marks the beginning of a larger ambition to build a series of pavilions - all enthusing conversations around material waste and how technology can play a part in righting current ecological wrongs.
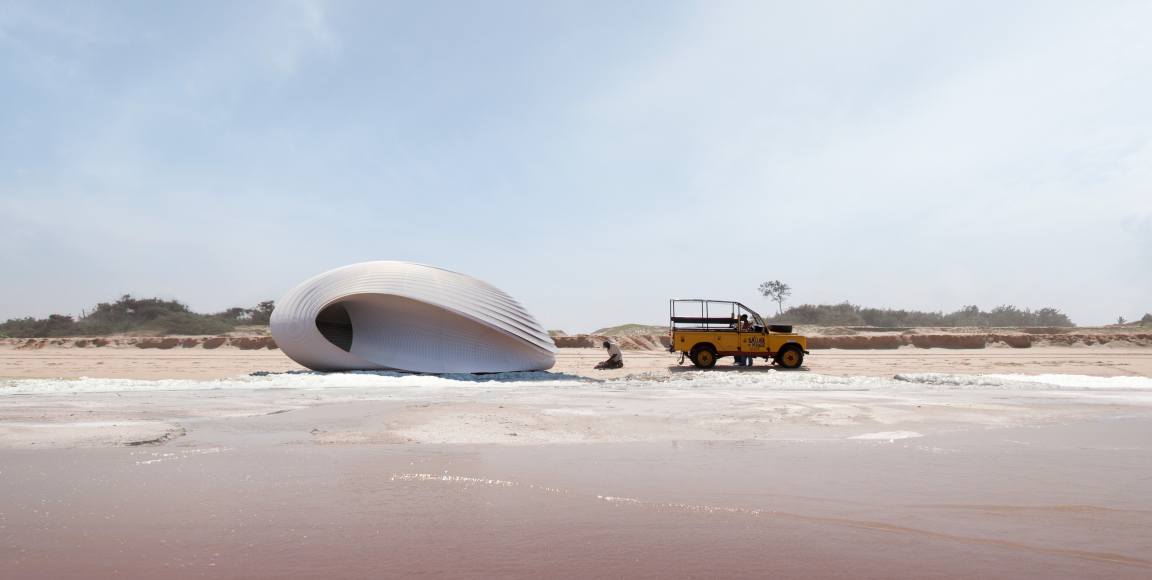
Hassell x Nagami: 3D printed plastic pavilion.
3. Tecla – A 3D printed global habitat for sustainable living
A new, circular model of housing - constructed from locally sourced soil - is fresh off the printer bed.
Constructed using raw earth and multiple printers at the same time, TECLA is blazing a trail towards a new, eco-conscious perspective for buildings and new settlements.
TECLA – a spin on the merger of technology and clay - is the concept of Mario Cucinella Architects and WASP. Developed with WASP's brand-new 3D printer in the construction sector, Crane Wasp the enterprise unifies one of one of the oldest materials with the most cutting-edge of technology. The material choices enable the model housing to be carbon neutral and adaptable to any climate or context.
Established in 2020 to break ground on approaches needed for 0km green housing, the project puts forward solutions to housing emergencies around the world, both in the built metropolis and in the instances of natural disasters and mass migration. Driven to better housing globally for people, TECLA seek answers for the Earth, in the earth.
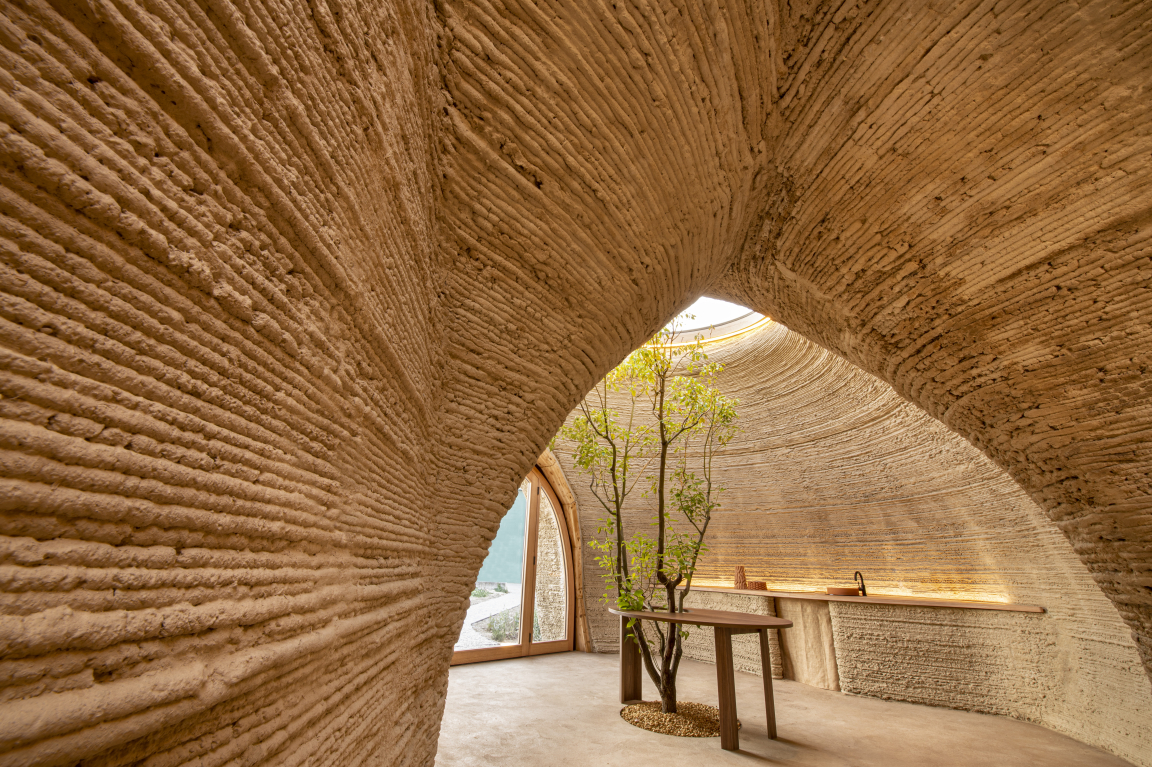
Tecla 3D printed house WASP + MCA interior.
4. Mamou-Mani x Fab.Pub – Sandwaves & Briar
Mamou-Mani is a unique architectural practice, producing digitally designed and fabricated architecture for an impressive portfolio of clients. Its offering doesn’t stop there. Highly detail driven, it also develops a wide range of custom products and interfaces to create truly immersive and otherworldly spaces that both inspire and uplift. Delving further into the possibilities of the digital world, it now offers parametric consultancy, as well as designs for the Metaverse.
With the materiality of its pieces being just as ambitious as form, Mamou-Mani interrogates the possibilities between the digital and physical worlds by constantly exploring new processes, technologies and implementing different biomaterials. Its own fabrication facility, FabPub, enables the team to trial and test previously unexplored making methods and materials.
Whilst embarking on projects such as Aurora - a bio-sourced PLA installation for the Design Museum’s well attended Waste Age exhibition, the practice showcases what is possible when biomaterials and 3D printing technology are merged.
It has also created site-specific artworks for the likes of COS for Salone de Mobile in Milan and developed the world’s largest 3D printed Sand Pavilion – The Sandwaves. And as an award-winning, international RIBA chartered practice, its innovative vision for the built environment is tangibly explored, re-defining the sector as we know it.
One of its more recent undertaking’s is a large-scale 3D printed chandelier for Virgin Hotels in Edinburgh. Briar - nicknamed as the Scottish Rose - illuminates a grand, gothic refurbished church.
The chandelier’s structure is inspired by stone tracery, a Centuries' old craft of carving ornate, curvilinear window frames in cathedrals. Fusing heritage crafts with cutting-edge technology and parametric design, Mamou-Mani transports lighting to the third dimension. The team has used a mixture of PLA - a bioplastic made from fermented sugar and brass powder - to empower new methods of circular thinking within interiors.
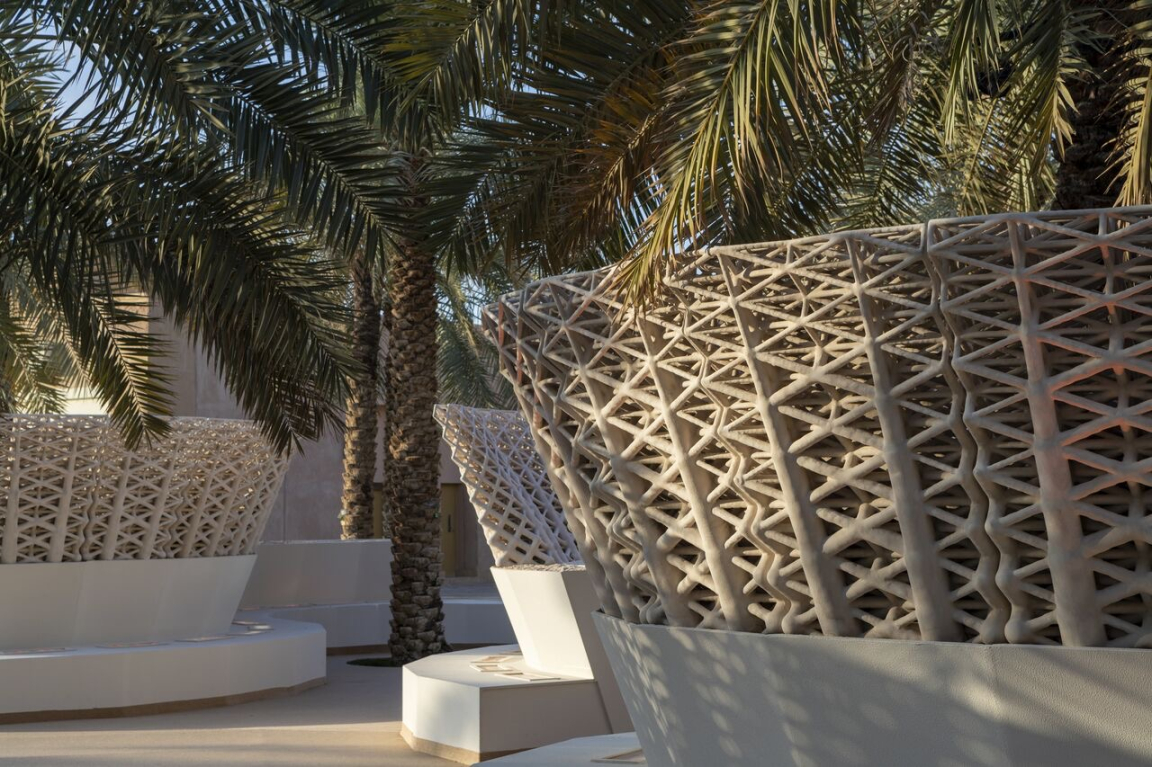
Studio Precht & Mamou-Mani - Sandwaves.
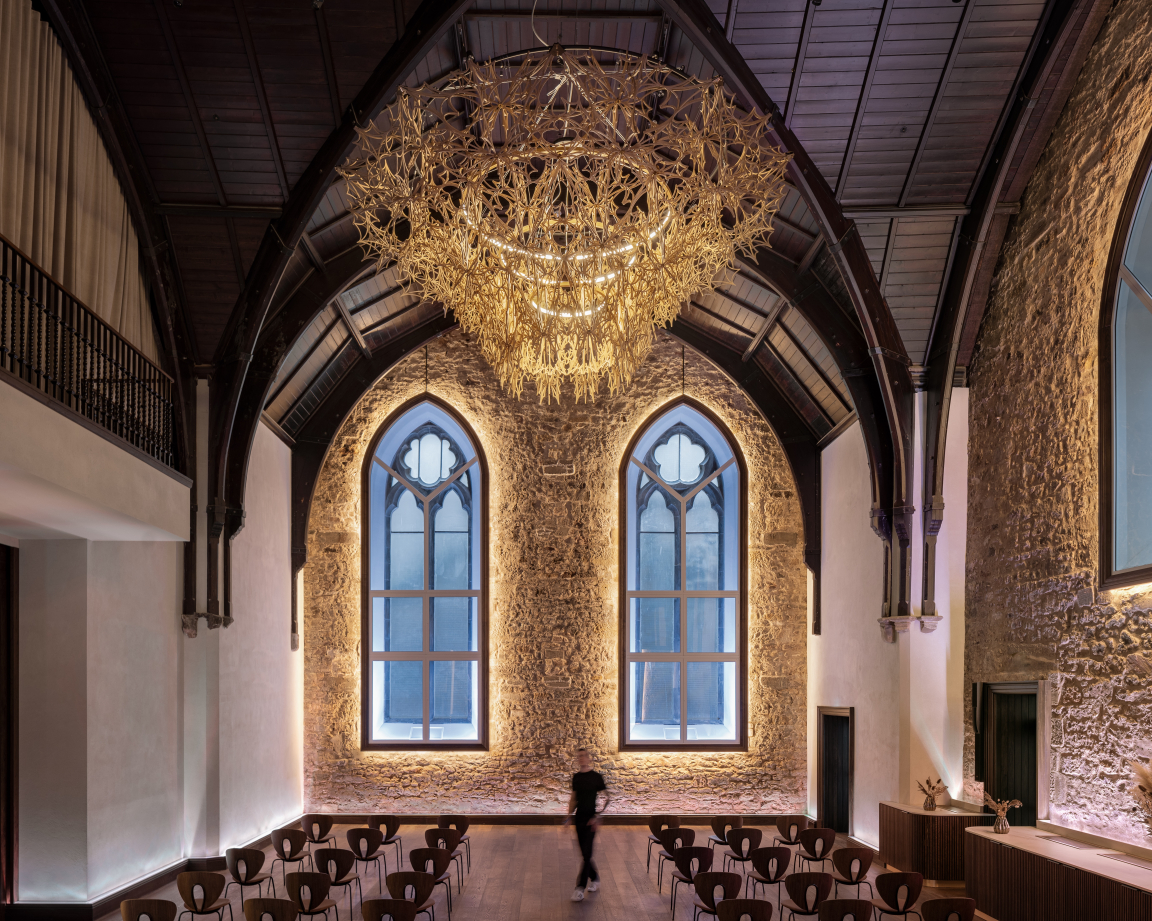
Mamou-mani: Briar.
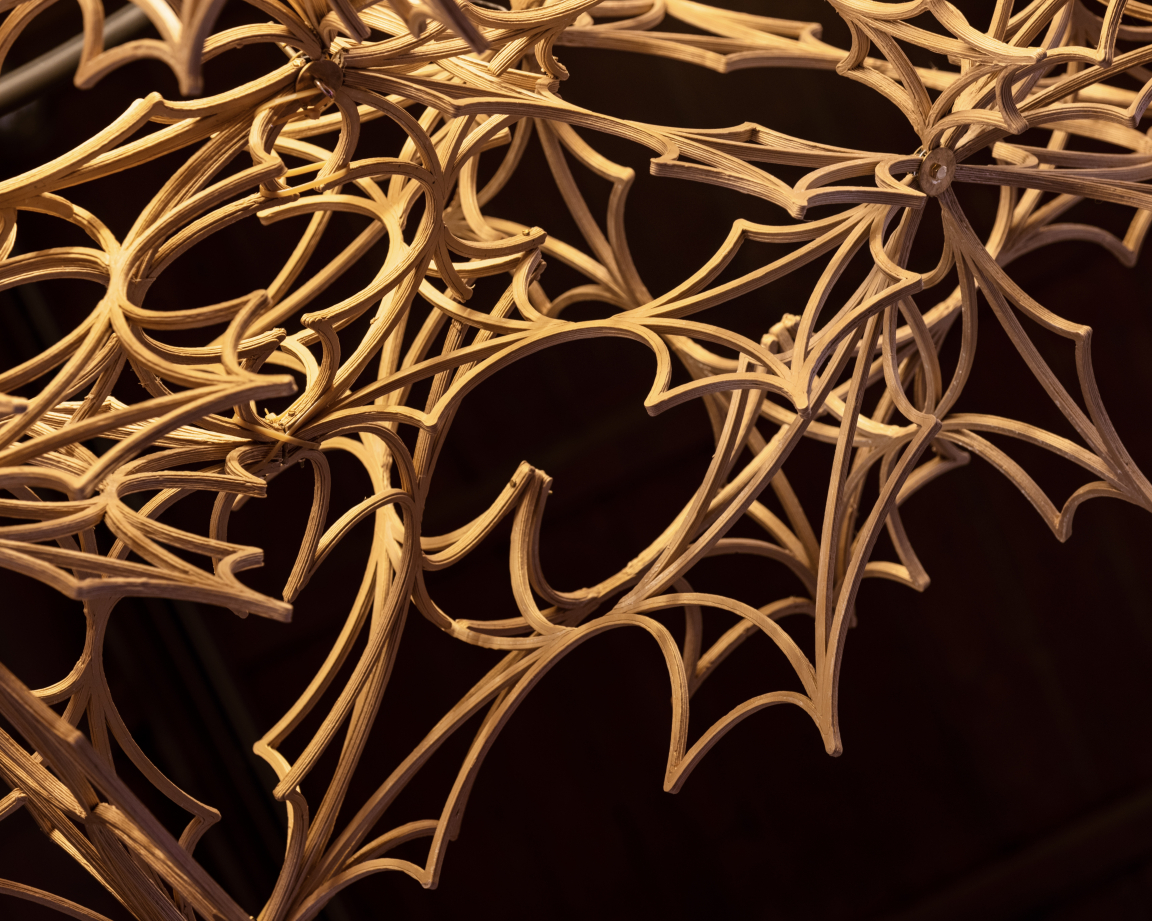
Mamou-mani: Briar.
5. Monisha Sridhara – Ceram-Screens
Perforated brick facades have a respected history in low-impact architecture, utilised across the world due to their advantageous environmental features. Unfortunately, over time through mass standardisation and industrialisation, these facades are limiting in functionality and typically lacking in character.
Recent graduate of the Bartlett School of Architecture’s Design for Manufacture course, Monisha Sridhara is probing the architectural potential of perforated brick façades from the perspective of 3D printing. Her project questions to what degree can extrusion-based additive manufacturing overcome the geometric limitations currently in place for perforated brick production technology and how 3D printing technologies can improve the interior lighting, ventilation, privacy and thermal comfort of a space.
Inspired by the traditional stone-carved 'Jaali' screens, Monisha was keen to implement their inherent functionality to manipulate sunlight, heat radiation, ventilation and privacy. The model has been designed for ease of manufacture, developed through continuous tests and refinement. The final prototype was assembled using cement mortar for the Bartlett Fifteen Show.
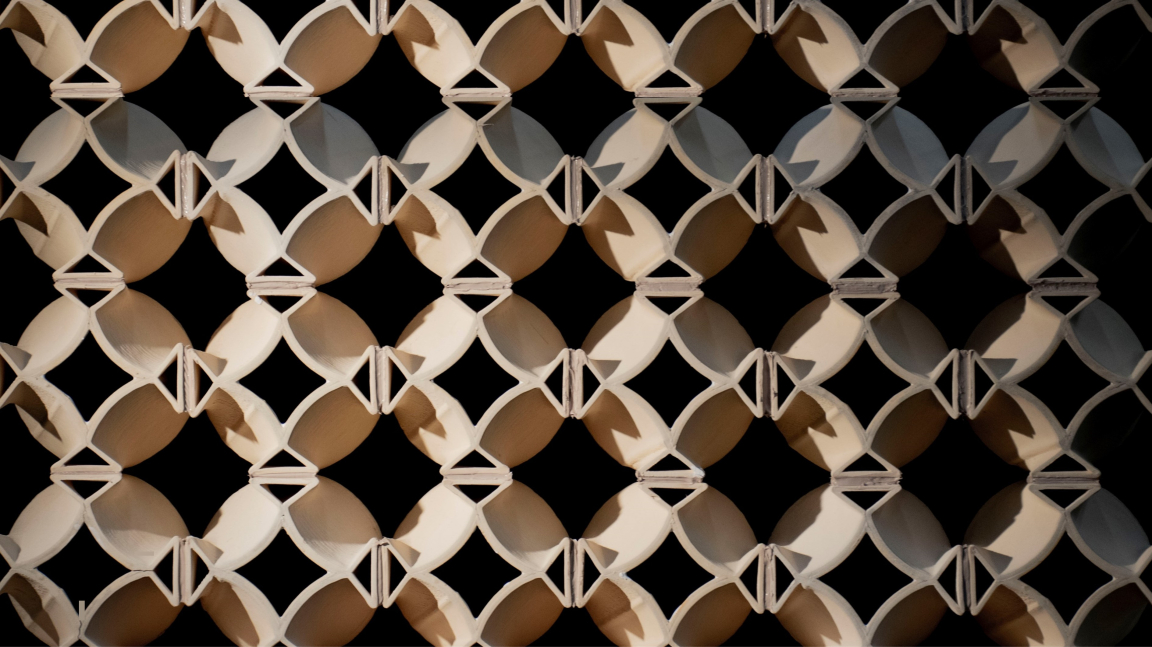
Monisha Sridhara: Ceram-Screens.
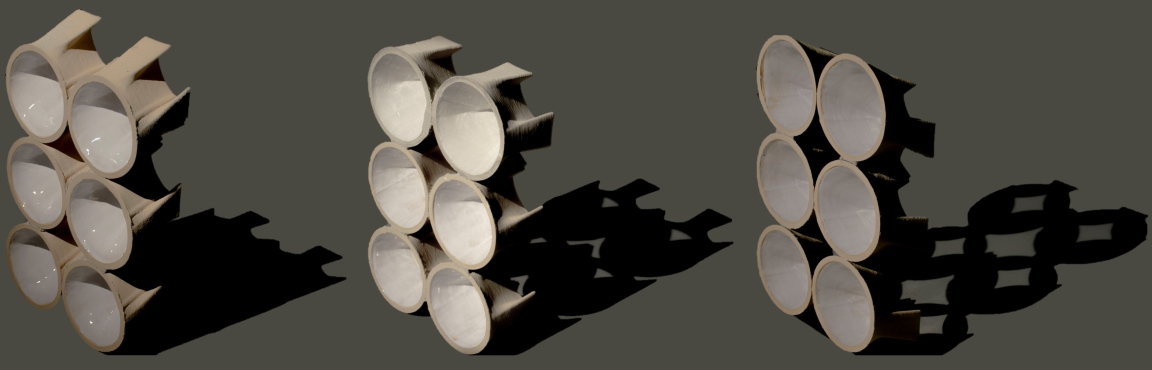
Monisha Sridhara: Ceram-Screens.
6. Julia Koerner – Crystal Lamellas & Stelae
Working at the intersection of architecture, product design and fashion, Julia Koerner is internationally recognised for pushing the boundaries of 3D printing technologies. Achieving her signature flowing, organic forms across all of her explored disciplines, the Austrian designer is celebrated across respected institutions and publications such as the Metropolitan Museum of Art and The New York Times.
Crystal Lammellas features a digitally crafted 3D design inspired by the surface qualities of the gills and lamellae of fungi. These digitally crafted glass sculptures are manufactured by Swarovski, through their glass 3D-printing technology. Julia has been collaborating with Swarovski over the last four years, focusing on design and sustainable manufacturing innovation.
3D Stelae are two digitally crafted columns, pushing new limits of what is architecturally possible with 3D printing technology. Printed in-house and in multiple segments using a weather resistant polymer, the columns stand up to the durability needed for exterior builds.
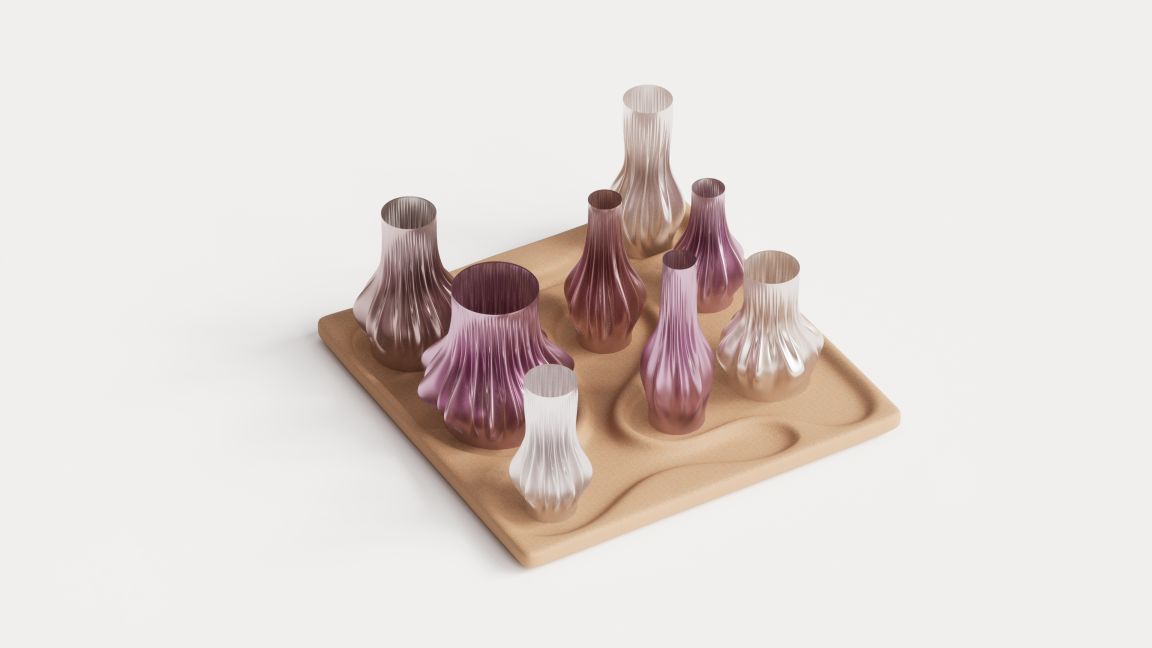
Julia Koerner: Crystal Lamellas.
7. ETH Zürich & FenX - Airlements
ETH Zürich FenX are pioneering new means of insulating and strengthening our built environment using cement-free mineral foams and digital fabrication.
Airlements is a collaborative research project, producing monolithic, lightweight and insulated wall constructions. These constructions are created by extruding diverted recycled waste through a large-scale robotic 3D printer - reducing the material, labour and cost typically involved when developing bespoke building parts.
This cement-free mineral foam produced by FenX has a lower carbon footprint than foamed concrete and plastic foams, and since it is one material with different densities, its properties facilitate the future reuse and recycling of building parts, whilst also providing insulation and strength. This all contributes to lowered operational energy costs for heating buildings.
Airlement’s robotic 3D printing system is developed at ETH Zürich in collaboration with FenX, its two-metre high assembly of four 3D printed parts being the largest prototype conceived in their research. Holding true to its claims of a low energy-intensive process, all constructed parts were 3D printed in under one hour and hardened for one week inside the fabrication environment. Its corrugated texture is a result of a path design that increases the strength during hardening of the structure.
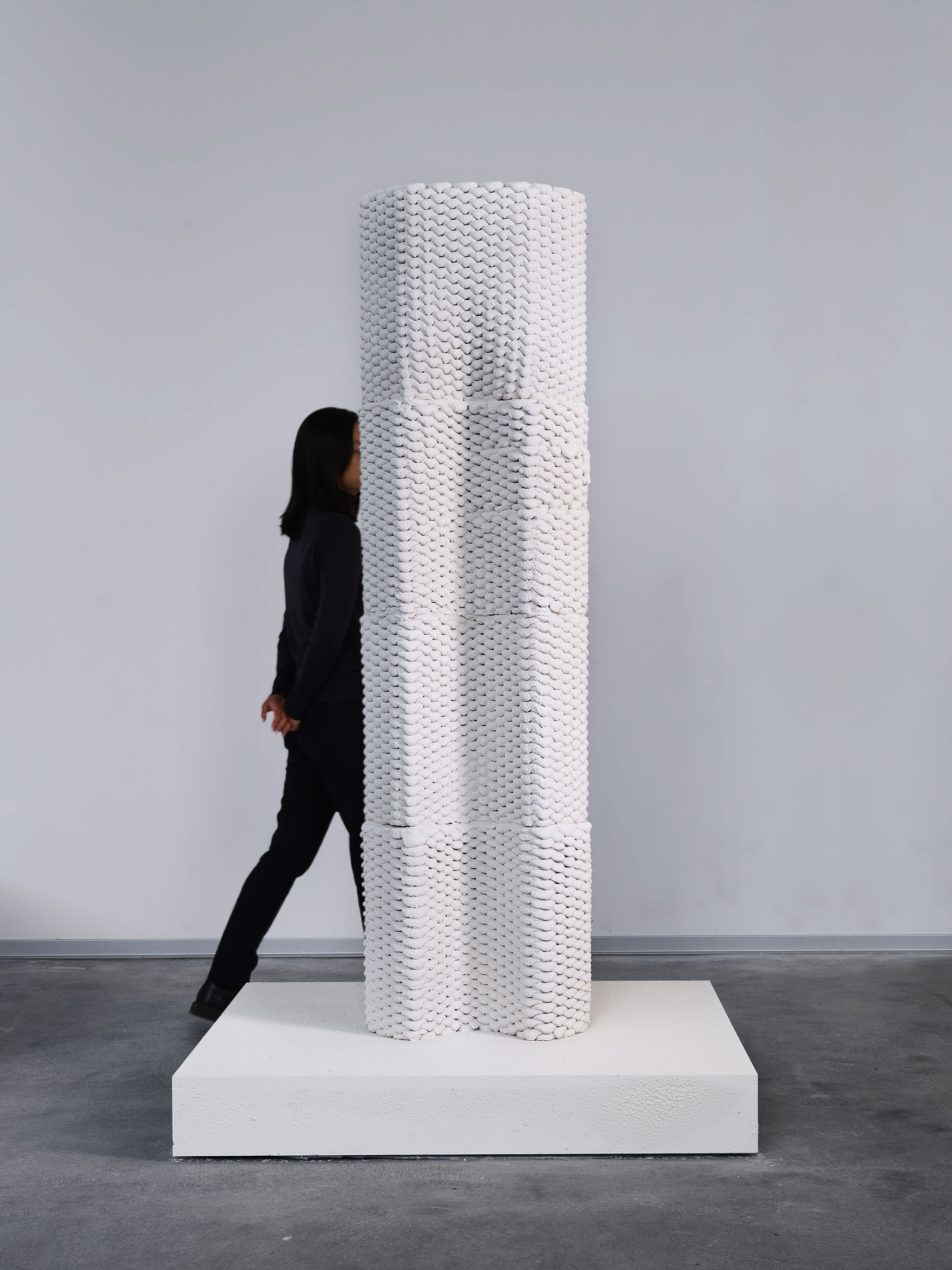
ETH Zürich + FenX AG: Airlements. Photography by Hyuk Sung Kwon

ETH Zürich + FenX AG: Airlements. Photography by Hyuk Sung Kwon.
Filament
Digital fabrication now takes many forms of materiality. Able to redirect both natural and synthetic by-products into re-envisioned tools, products, buildings and works of art, 3D printing technology is significantly boosting circular and regenerative design processes across sectors.
8. The New Raw – Knotty & The Loopy Chair
This practice does exactly as it says on the tin. Founded by architects Panos Sakkas and Foteini Setaki, The New Raw has set out to make plastic waste the new raw material for the creation of one-of-a kind, meaningful objects. Based in Rotterdam, the team gives new life to discarded materials through design, robots and craftsmanship – one print at a time.
Released at Milan Design Week last year, its project Knotty takes inspiration from soft, tactile knitted textiles, producing a collection of playful benches with a bold and tactile texture.
Inspired by knitting techniques, the project treats plastic waste as a continuous golden thread of material which folds, twists and loops to create an intriguing tactile surface. The sculpted material texture - consisting of thick and seemingly soft knots - creates a tactile, permeable and load-bearing surface type for outdoor and indoor furniture or other architectural applications.
This body of work was re-visited for the Material Matters Fair at London Design Festival late last year. Through collaboration with British Furniture designer, Gareth Neal, ‘The Loopy Chair’ is fabricated from a three times recycled polymer in a series of interlocking loops as a part of the ‘Digitally Woven’ study.
The Loopy Chair explores the merger of additive manufacturing and furniture production with traditional crafts such as knitting, crochet and weaving. This loop lathered lounge chair is suitable for both indoor and outdoor use, and inflicts an intense sense of tactility.
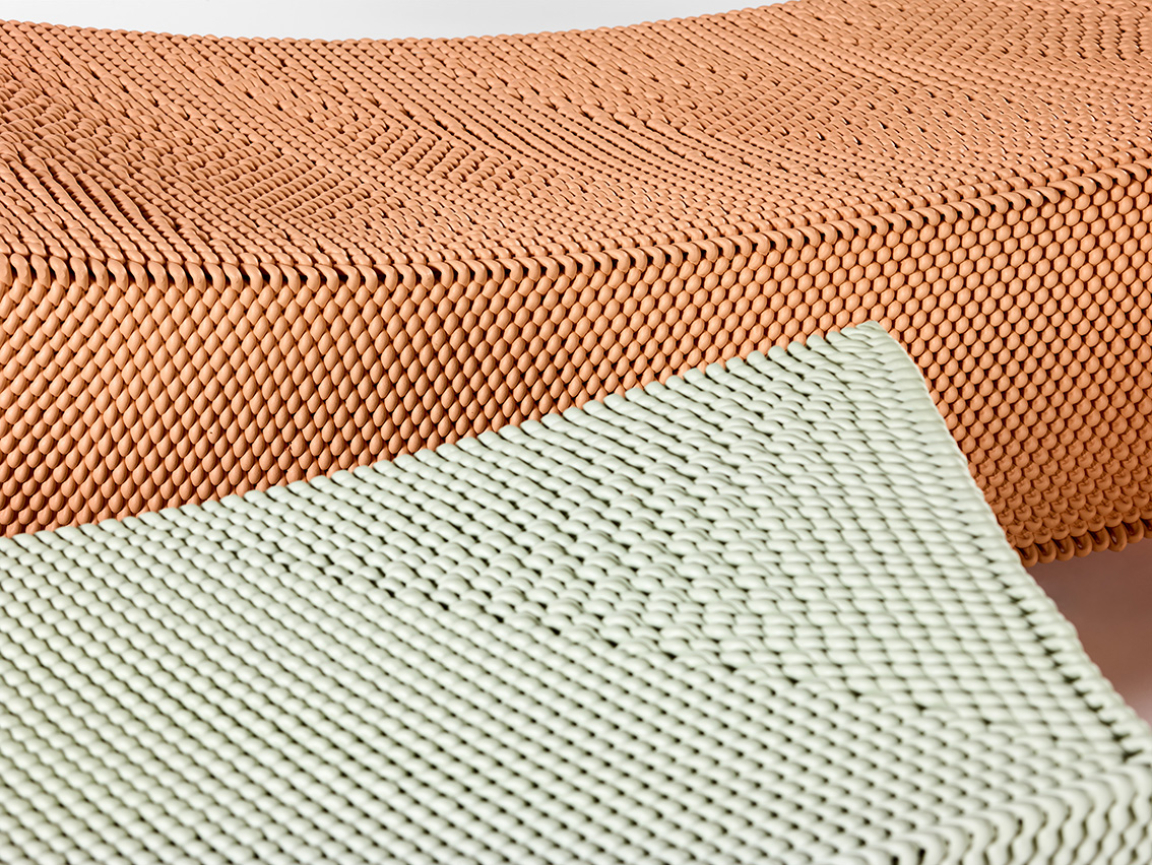
The New Raw: Knotty.
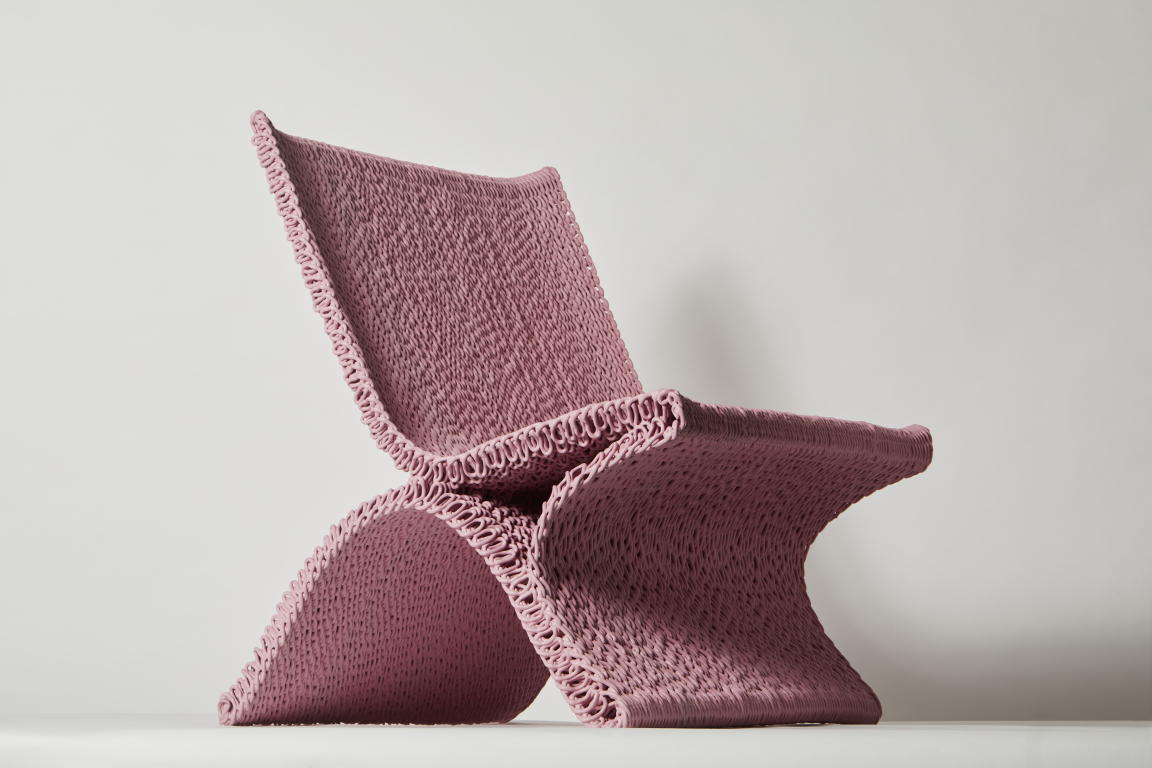
The New Raw + Gareth Neal Furniture: The Loopy Chair.
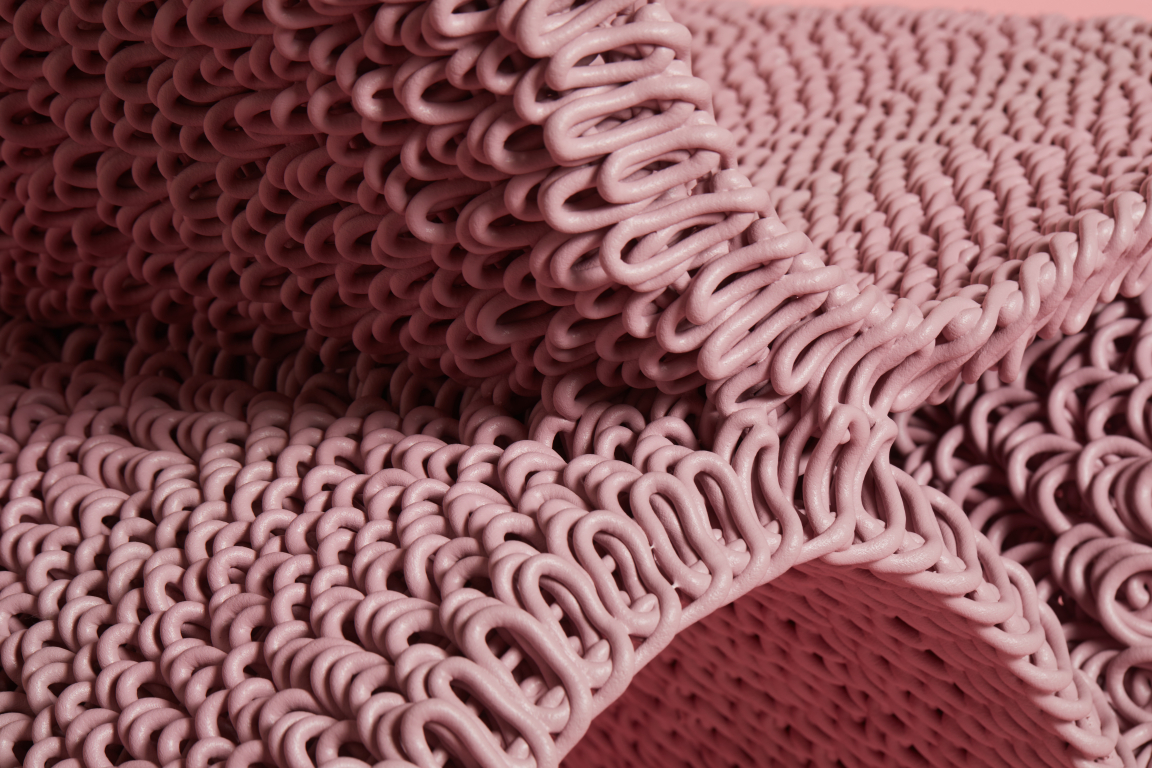
The New Raw + Gareth Neal Furniture: The Loopy Chair.
9. Isaac Monté – Bio-based printing with self-engineered nozzles
Rotterdam based designer-maker, Isaac Monté blends art, science and product design for his eclectic practice. Fascinated with societal sustainability, Isaac reveals hidden qualities and uses in discarded materials.
His practice uncovers beauty in the most unfavorable of waste-streams - fashioning striking sculptural lighting from thrown away and then decellularised meat, and growing crystallised vases in enormous, caldron-like vats in his studio.
Isaac has recently been expanding applications of bio-based materials through additive manufacturing – and engineering his own 3D printing equipment to do so. Revealed at Dutch Design Week in Eindhoven, Isaac presented his developments in 3D printing bio-based pastes with the waste-streams of the picked fruit industry and limestone industry.
Producing a calcium-based paste from his investigation into limestone and stone masonry, Isaac’s digitally constructed clams symbolise a synthesis between heritage craft and additive manufacturing technologies. Through trial and error with his material developments, Isaac determined he would need to design and produce his own nozzles to extrude the unique bio-based pastes.
The Netherlands throws away an astonishing 1.3 billion tonnes of food produce each year, with 45% of all fruit produced for consumption being discarded due to rot and bruising from its long journeys across international waters. Confronting yet another linear system, this series of 3D vessels redirect the large quantities of imported exotic fruits and vegetables into functional objects for the home.
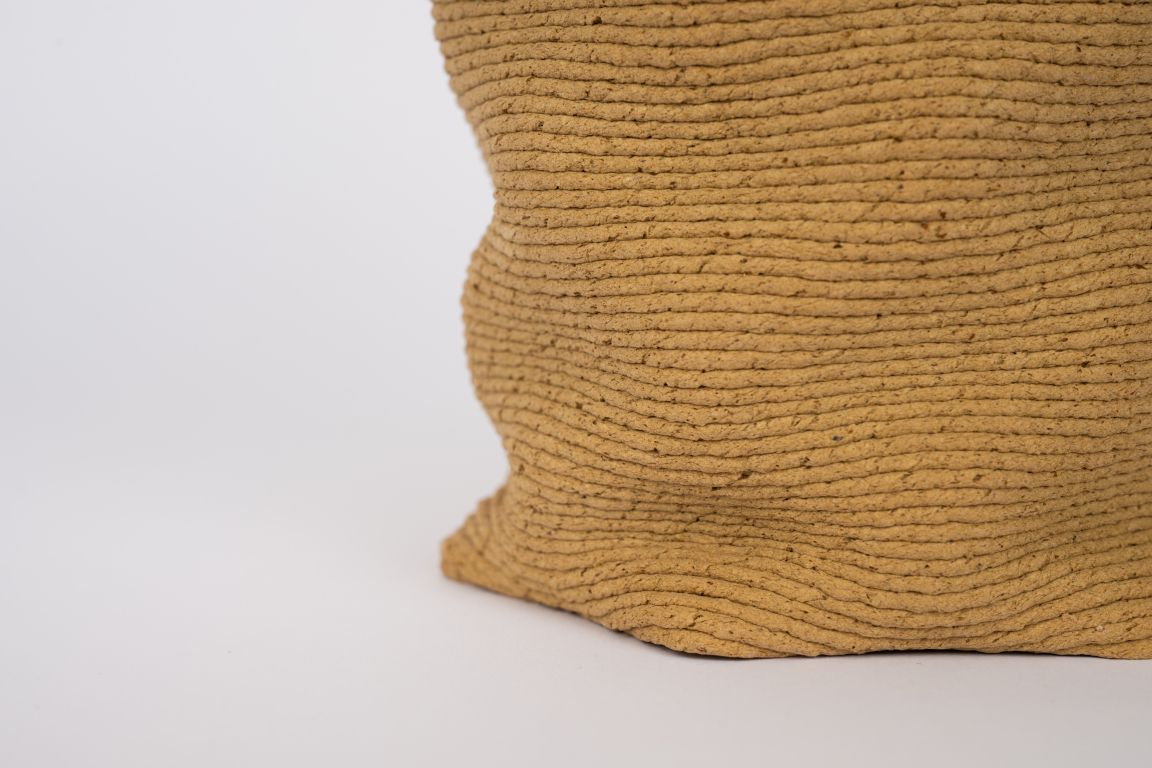
Isaac Monté: 3D printed fruit waste. Photography by Monica Monté.
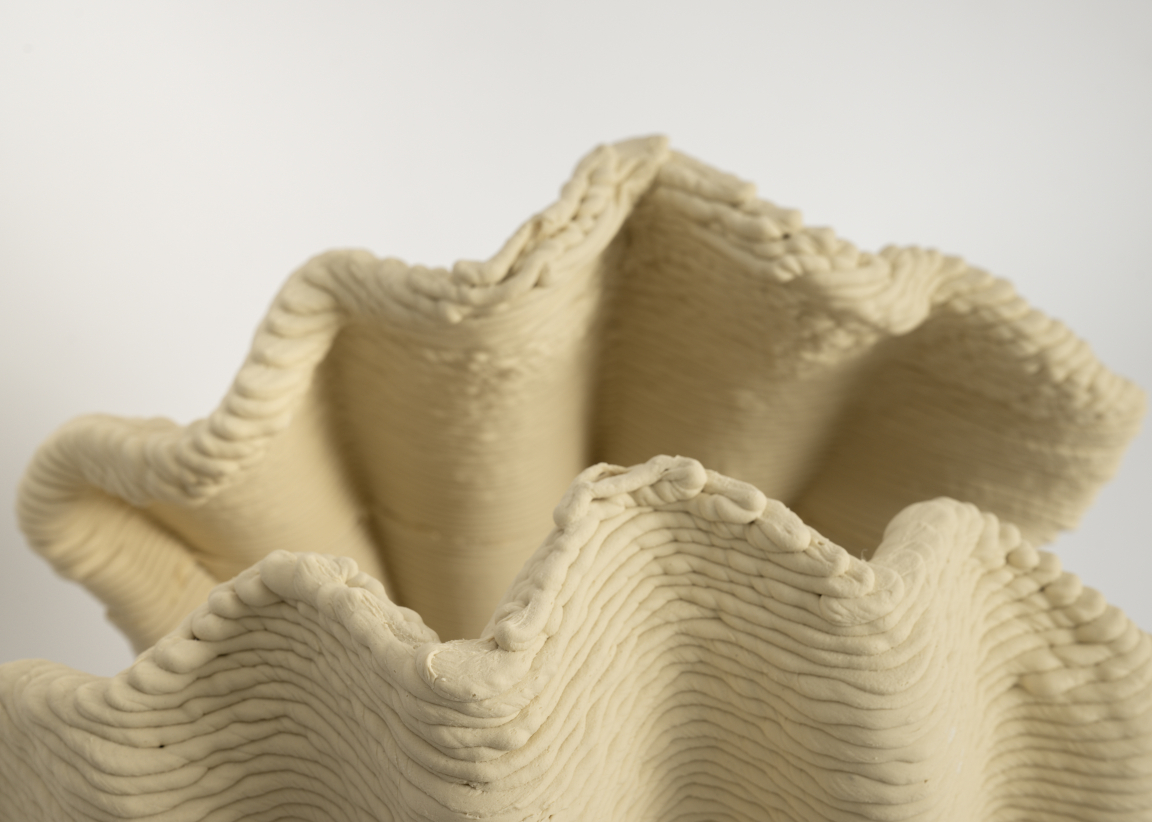
Isaac Monté: Stoneprinting. Photography by Monica Monté.
10. Gramazio Kohler – Clay Rotunda
Gramazio Kohler Research is the inquisitive institution behind Clay Rotunda – a free standing earth-based structure that explores the use of earth derived aggregates in reducing overall material consumption in the construction industry.
In its research, it meticulously examines shifts in architectural production requirements that result from introducing digital manufacturing techniques - with its specialty being combining data, material and the resulting implications this has on architectural design.
Gramazio Kohler Research blend traditional knowledge of clay constructions with contemporary digital design and fabrication processes in order to develop Clay Rotunda. By applying an increased degree of control, the project demonstrates how 3D printing can push us beyond what has been traditionally architecturally possible.
Different compositions of clay, sand, small stones and water have been tested to seek out the best balance between the malleability, strength, and minimal material shrinkage. The developed clay mix is extruded into soft bricks, which are then picked up by a custom designed robotic arm, precisely oriented, and sequentially pressed into their final position.
No material is wasted in the process. Clay also boasts excellent properties in regulating the interior climate of buildings, thus reducing the need for mechanical ventilation - creating comfort for all inhabitants.
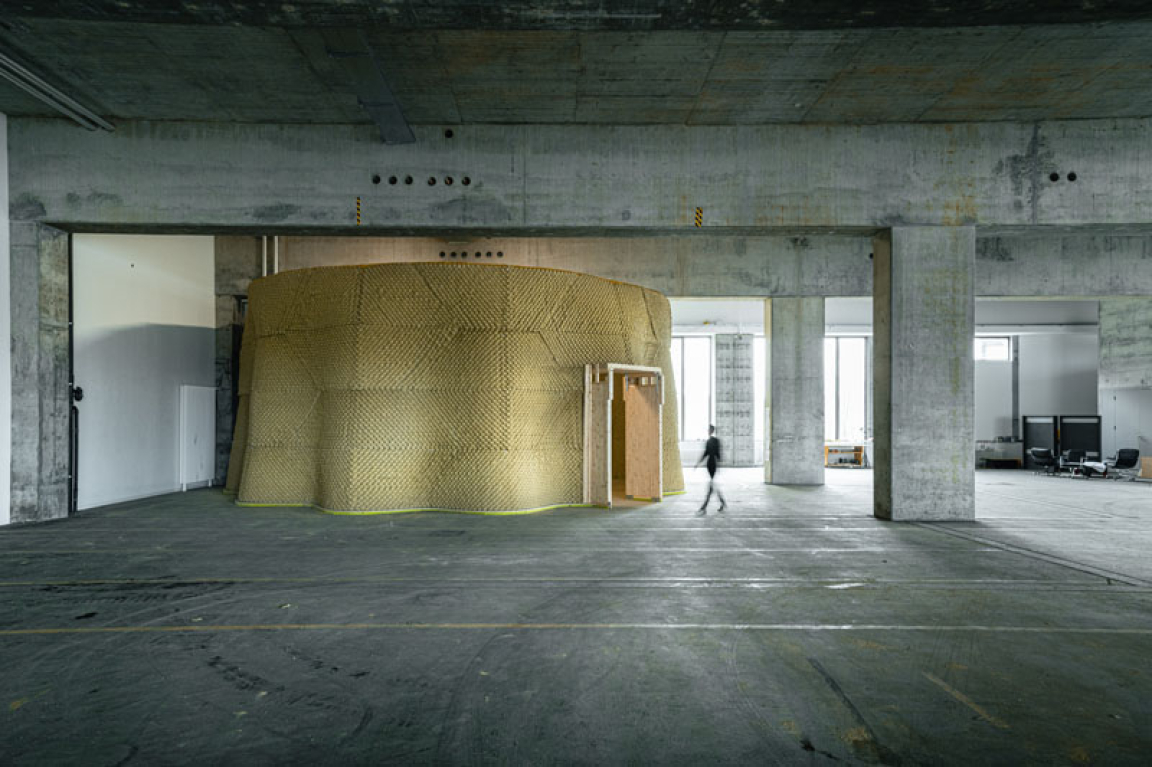
Gramazio Kohler: Clay Rotunda.
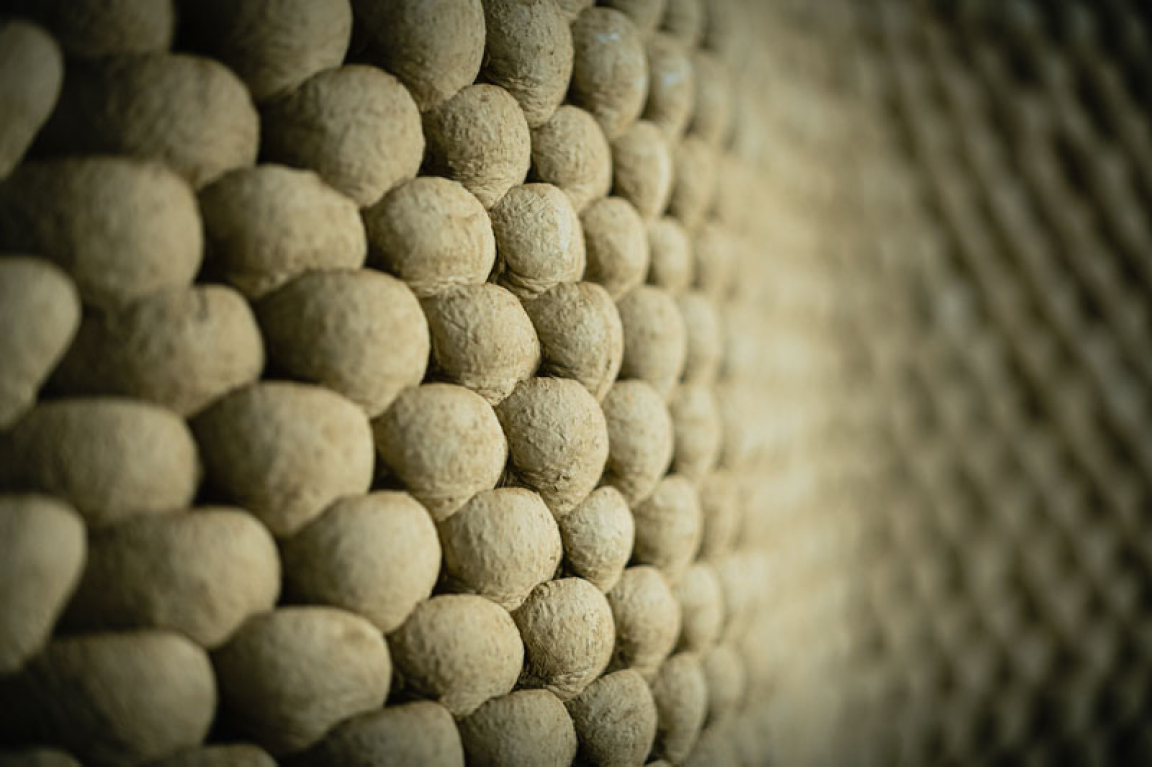
Gramazio Kohler: Clay Rotunda.
11. bioMATTERS - Bio-digital Craft
bioMATTERS is a research and design studio working at the intersection of digital and bio-based fabrication.
In response to the ecological crisis of depletion of natural resources and growing landfills of wasted materials, bioMATTERS is cultivating and manipulating living cells from mycelium, lichens, soil, bacteria and algae into scalable, 3D printed, bio-composite materials.
Based between New York City and London, its team has engineered interdisciplinary workflows that harness biological systems and additive manufacturing to create bio-fabricated textiles, products and architectural material systems. Additionally, it has developed a palette of living-based pigments used to add colour in some of its designs.
The primary ingredient of its products is up-cycled waste materials, with minimal waste involved in the bio-fabrication process.
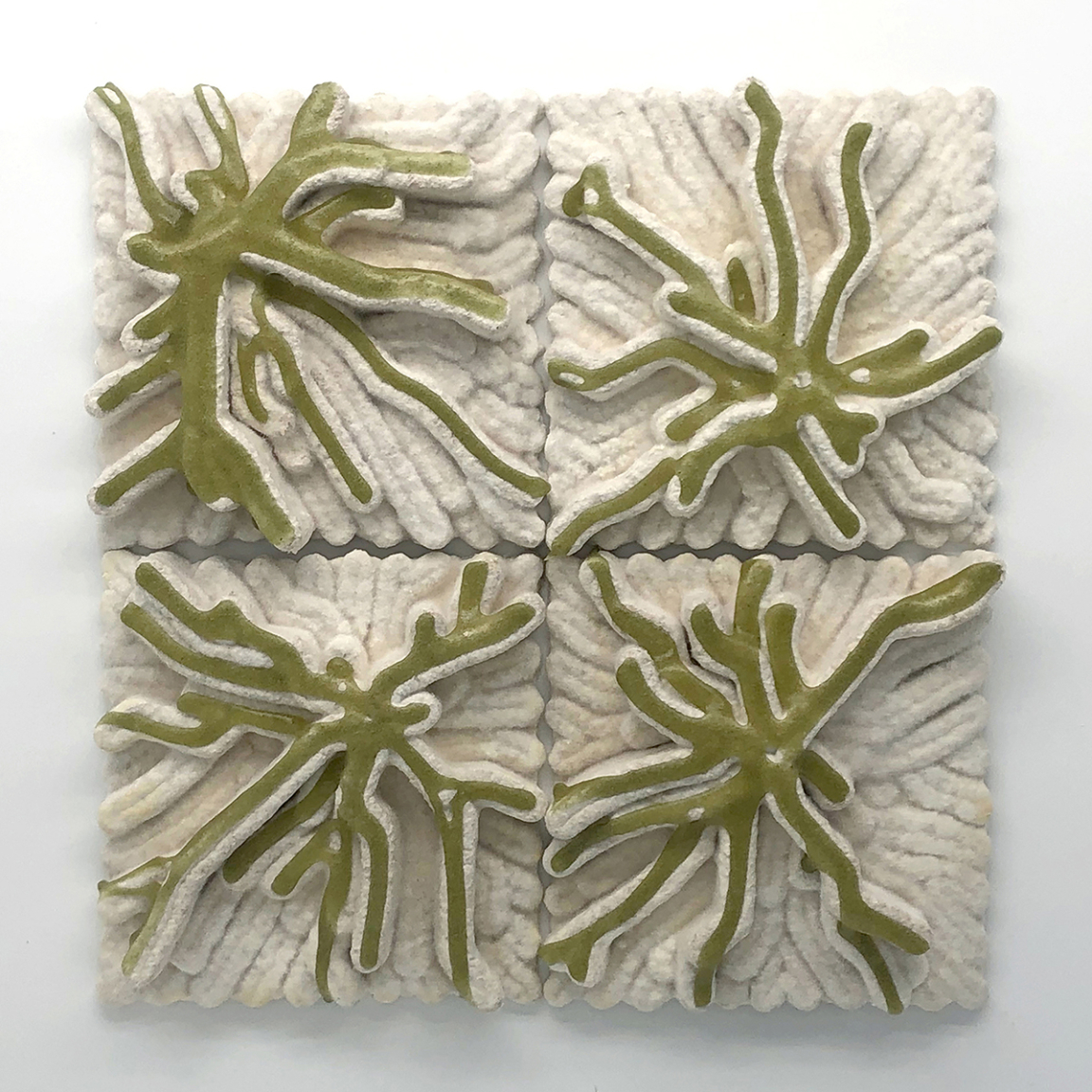
bioMATTERS: MYCO ALGA.
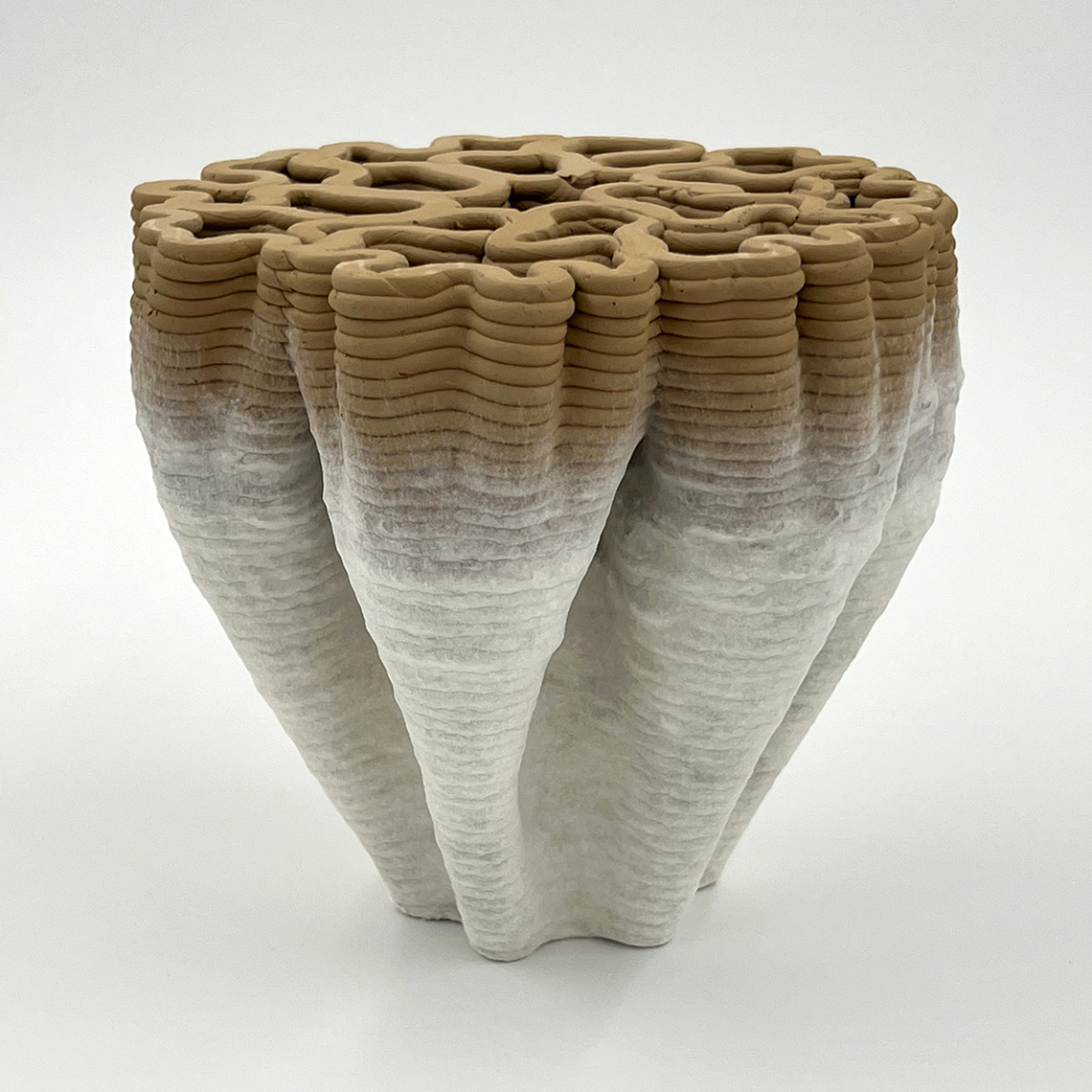
bioMATTERS: MYCO CLAY.
12. PrintCity – Full Circle Concrete
Tackling this ecological crisis of the concrete industry is the 3D additive and digital manufacturing hub, PrintCity.
Housed in the industrial heart of Manchester, their collaborative team of manufacturing experts, designers and engineers continually push the boundaries of 3D printing technology. PrintCity’s groundbreaking project, CIRMAP explores the architectural potential of concrete waste, excavated from construction sites across Europe.
CIRMAP is an Interreg North-West Europe funded project, focused on developing 3D printing mortars using Recycled Fine Aggregates (RFA). In North-West Europe, 65 Mt of RFA is generated annually from demolition waste, whereas 54 Mt of sand is extracted from marine environments.
A number of partner organisations across Europe worked in collaboration to demonstrate a successful application of RFA, developing a new mixture proportioning method with RFA. The results were 25 customised street furniture designs, planned to be installed in cities across North-West Europe.
Currently exhibited in Material Source Studio, Manchester, we are proud to provide a platform for solutions such as this, being put forward to help close the loop on the construction industry.
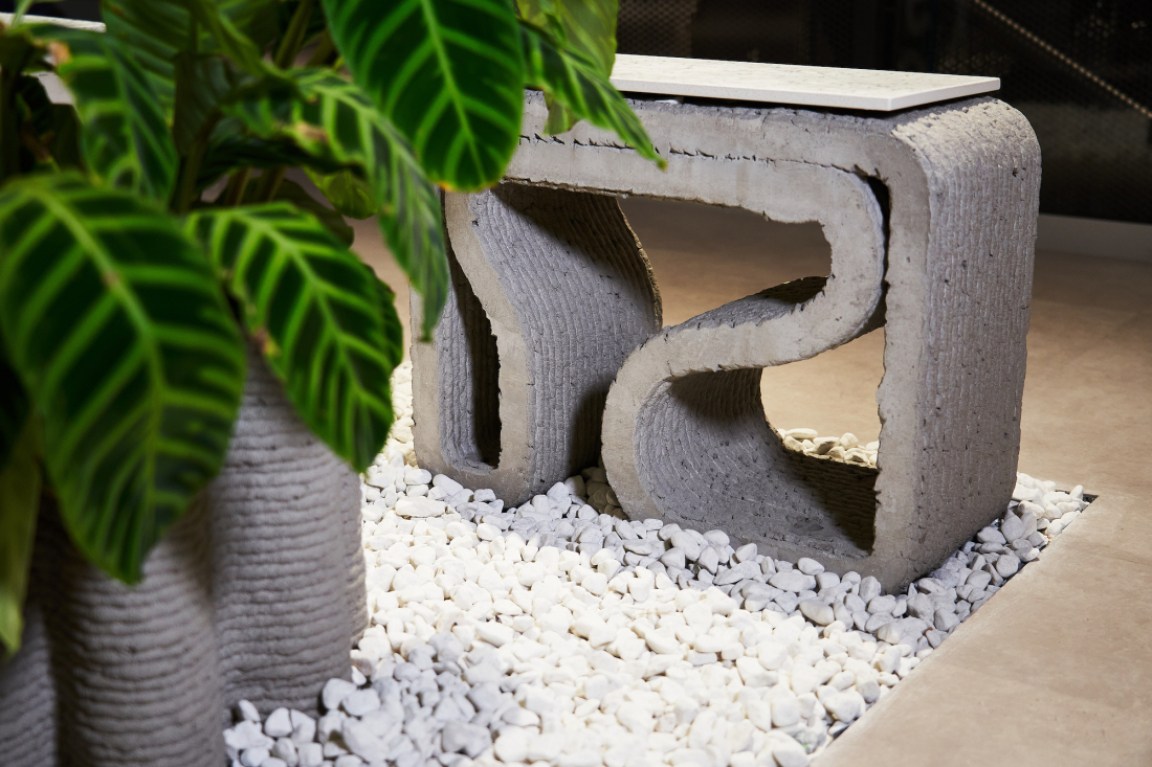
PrintCity - CIRMAP. Photography by Tim Ainsworth
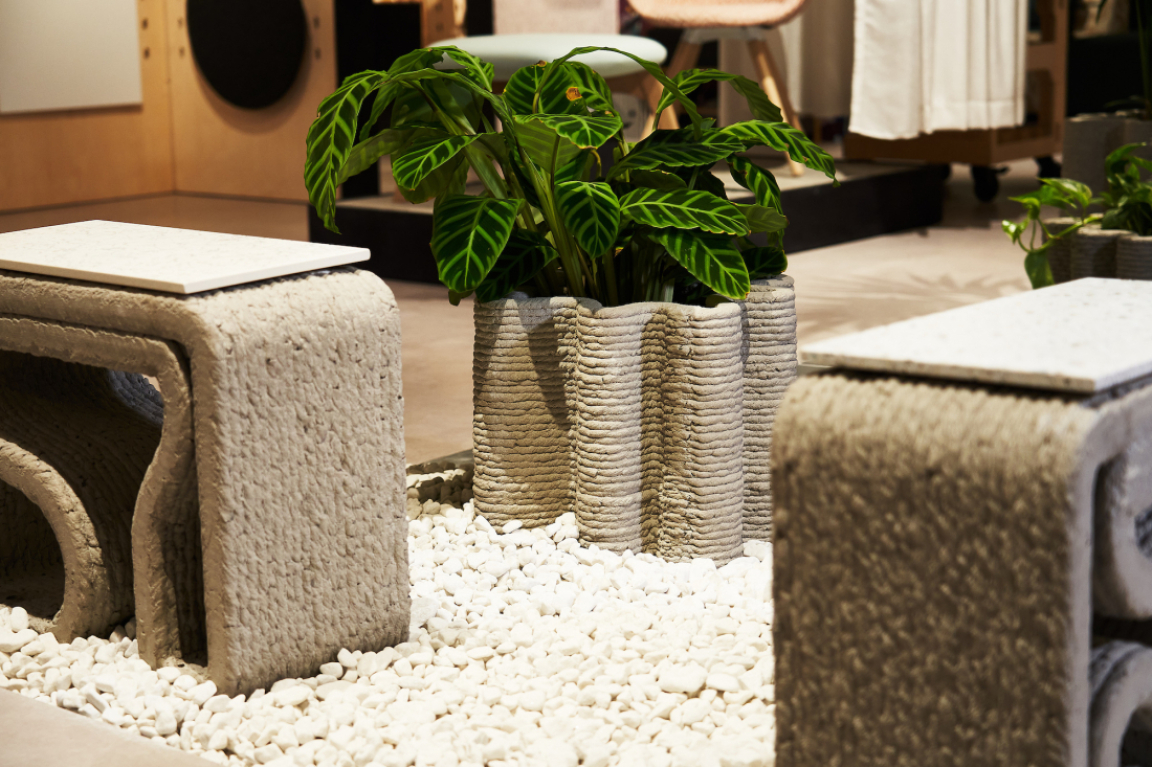
PrintCity - CIRMAP. Photography by Tim Ainsworth.
13. Ori Orisun Merhar – Made By Insects
Ori Orisun Merhar is the artistic researcher and designer behind the design industry’s first insect derived 3D printable filament.
Ori caught our attention in the Design Academy Eindhoven showcase at 2022's Dutch Design Week. Her thesis calls for broader research around sustainable alternatives to fossil-based or toxic materials. Through her practice, Ori coaxes us to re-think the way we use the resources around us and to foster ecologically mindful approaches.
Upon a trip to Thailand, a fascination with the insects who are producing this natural polymer, 'Kerria Lacca' was born. Inspired to explore the structural possibilities of this material that insects use to build their shelters on tree branches, 'Lac-Lab' was set up. Lac-Lab is an initiative that invites different craftspeople to take part in the research, and it's here that designers learned the material lends itself structurally to the process of glassblowing.
Since then, her material pursuits with the natural polymer, Kerria Lacca have pushed further than just glass-blowing, she is now also 3D printing with it. Achieving delicate structural forms that glisten gorgeous amber hues, these are officially the first objects to be printed out of an insect produced polymer - with Ori blazing a trail on what we consider possible of 3D printed materiality.
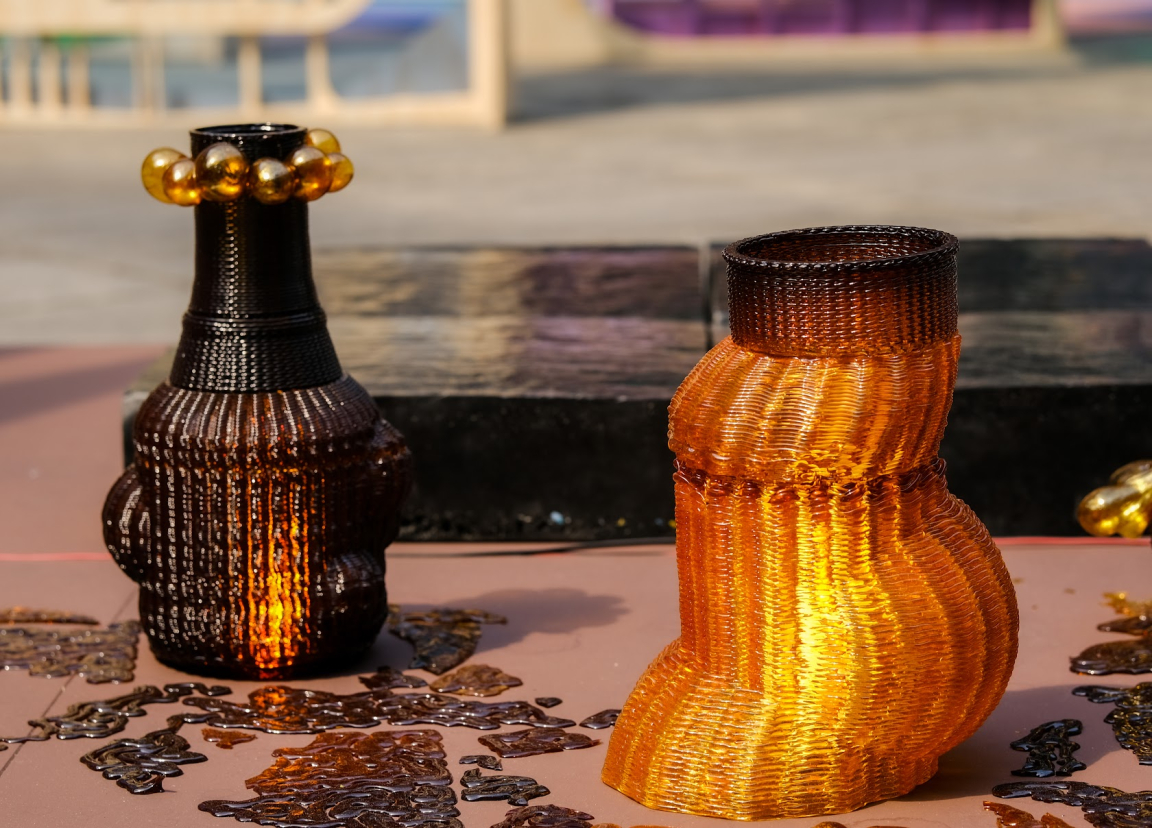
Ori Orisun Merhar: Made By Insects.
14. ITG – The Kelp Collection
Tackling ocean pollution face on is the Swedish practice, Interesting Times Gang. Commissioned by two-star Michelin chefs, Nicolas Jönsson and Daniel Höglander to design a chair inspired by their new sushi restaurant, Black Milk Sushi – the team went away and brought the swaying forms of ocean vegetation to function.
Excavated from the Baltic Sea, recycled fishing nets and end-of-life maritime gear are combined with wood fibre to create a 3D printable filament. Each chair is 100% recyclable and can be ground down to create new products within a closed-loop system.
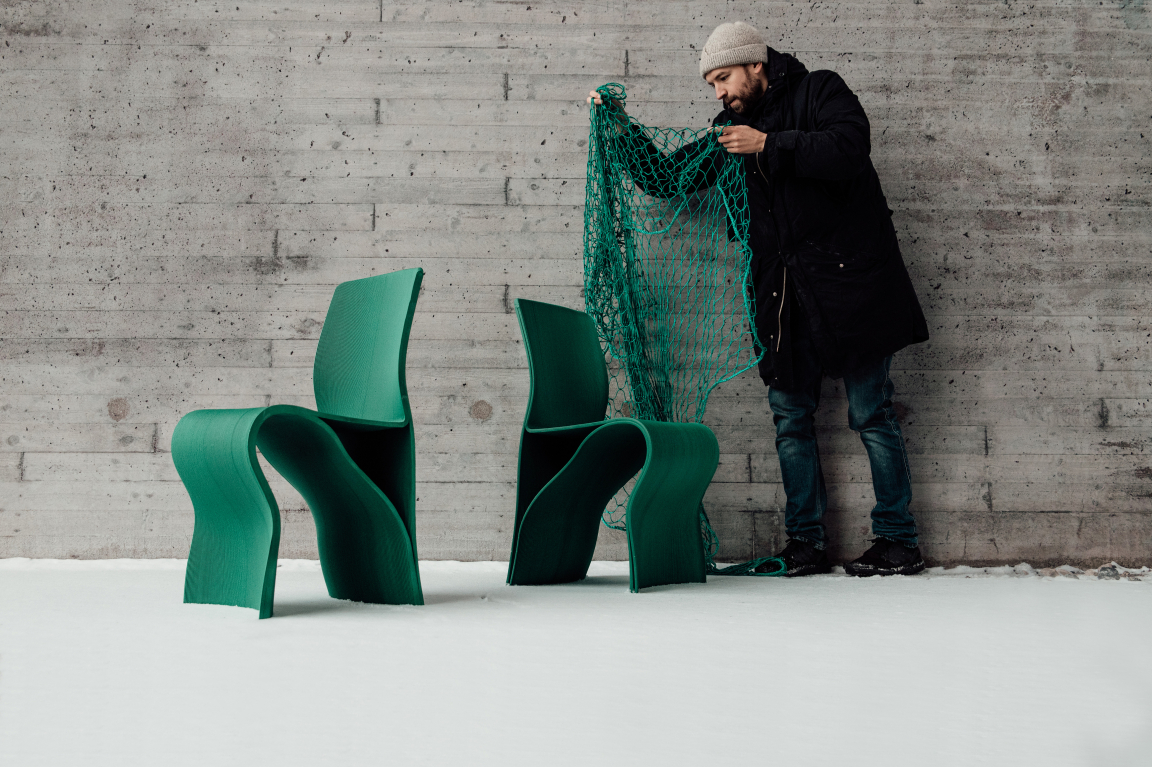
ITG Studio: The Kelp Chair.
15. Carbon Forest Products - Atmospheric Carbon 3D printing
Carbon Forest Products is the innovative start-up of Royal College of Art Product Design alumna, Patrick Morris. Through harvesting atmospheric carbon from trees, Patrick has developed the world's first 3D Carbon Composite printing process.
Carbon Forest Products' unique process uses lignin power - a renewable, low cost by-product of the paper manufacturing industry - to create a sustainable, high-performance powder which can be 3D printed into geometries using a selective laser sintering process. The benefit of using a selective laser sintering process is that it produces a much higher resolution, and the surrounding powder is self supporting of the printed structures, so no need for scaffolding.
Its 3D printed carbon composite has a wide range of potential applications; including thermal management, electric vehicle heat exchangers, commercial drone technology, and could be valuable to a host of different industries, such as automotive and aerospace.
Carbon Forest Products are focused on unlocking the enormous potential in mass 3D printing, especially in applications where lightweight, thermal and electrical conductivity and material stability are paramount.
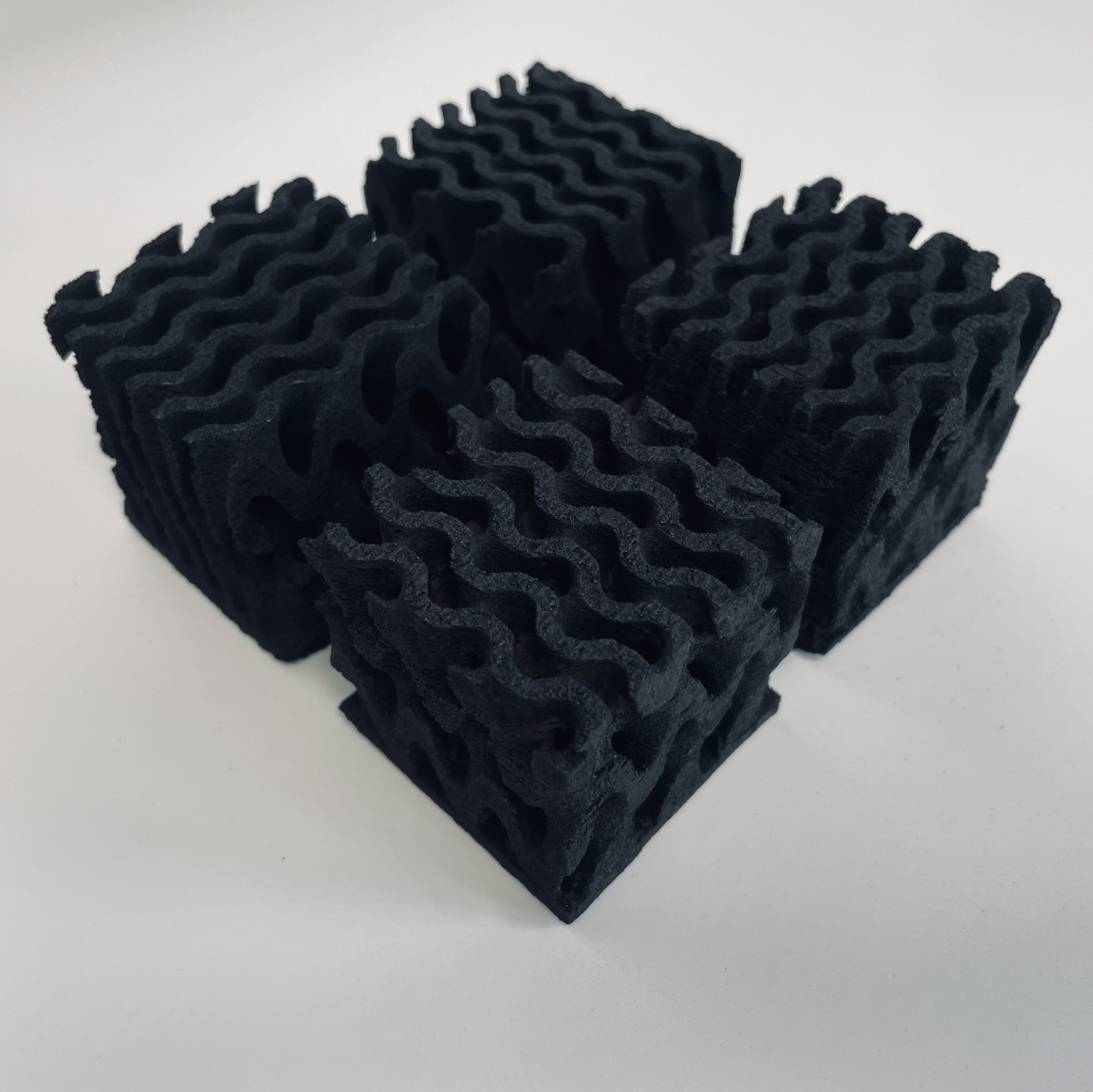
Carbon Forest Products.
16. Lowpoly – The Tyre Collective
A plethora of pollution derived products and solutions were exhibited at Material Matters Fair during last year's London Design Festival. Driving the repurposing of tyre waste is a team of talented creators; The Tyre Collective, Rafael El Baz, Qiang Li, Lowpoly, and Queen Mary University of London's Material for Sustainability Group.
These synthetic rubber particulates are a major micro-plastic pollutant on land and sea, negatively impacting on both human and planetary health. The collective of designers used a 3D printed filament of 20% tyre particulate and 80% recycled PLA to fabricate a range of products including; an acoustic panel, speaker and a lamp to re-direct this troublesome pollutant into a more circular system.
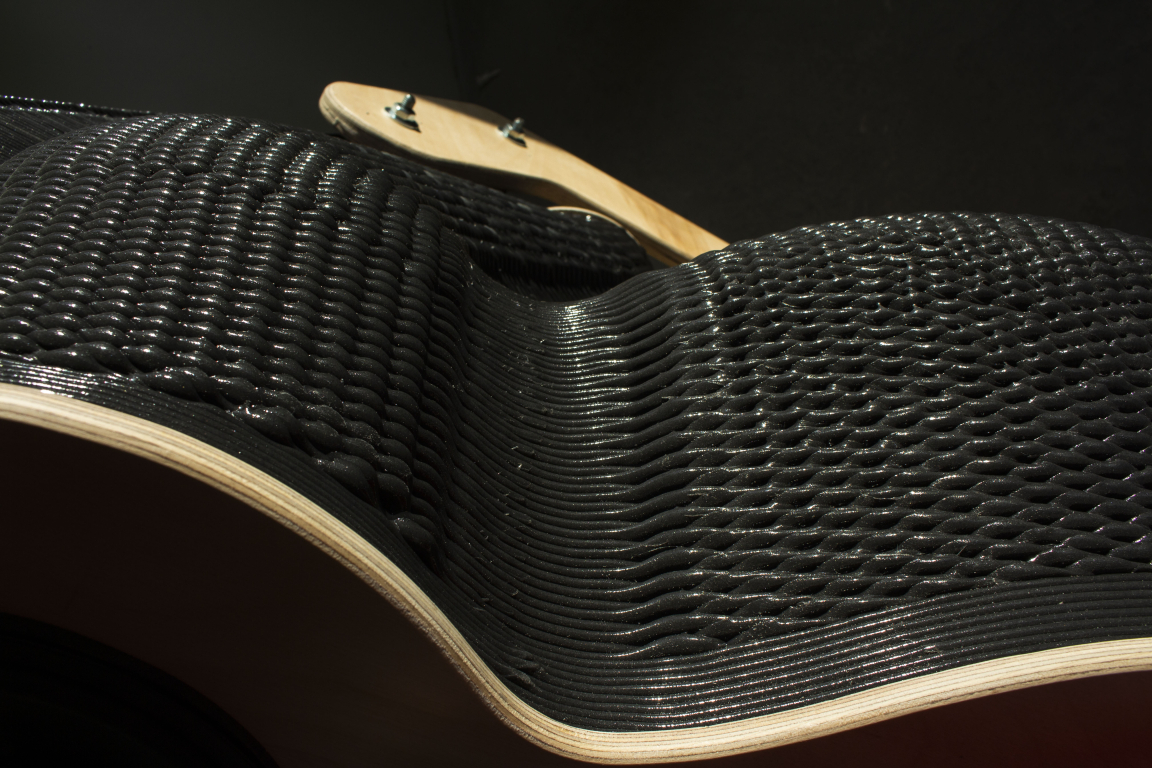
Lowpoly & The Tyre Collective.
17. Erco Lai & Sandhelden – Tafoni
Tafoni is the 3D printed vase of industrial maker and designer, Erco Lai. Influenced by the weathering and eroding nature of stone surfaces, Erco transforms these tactile qualities into digitally fabricated objects. Tafoni is created in collaboration with Sandhelden, a 3D printing facility that produces custom solutions for architecture, art and design - all printed from sand.
Offering the choice of three tonal qualities, each print in this sand-based filament offers a unique blend of nature inspired aesthetics within digital manufacture. Sandhelden invites a number of artists and designers that work with cutting edge media and creative technologies to collaborate with them, in order to explore new form, surface qualities and practical applications of their developed filament.
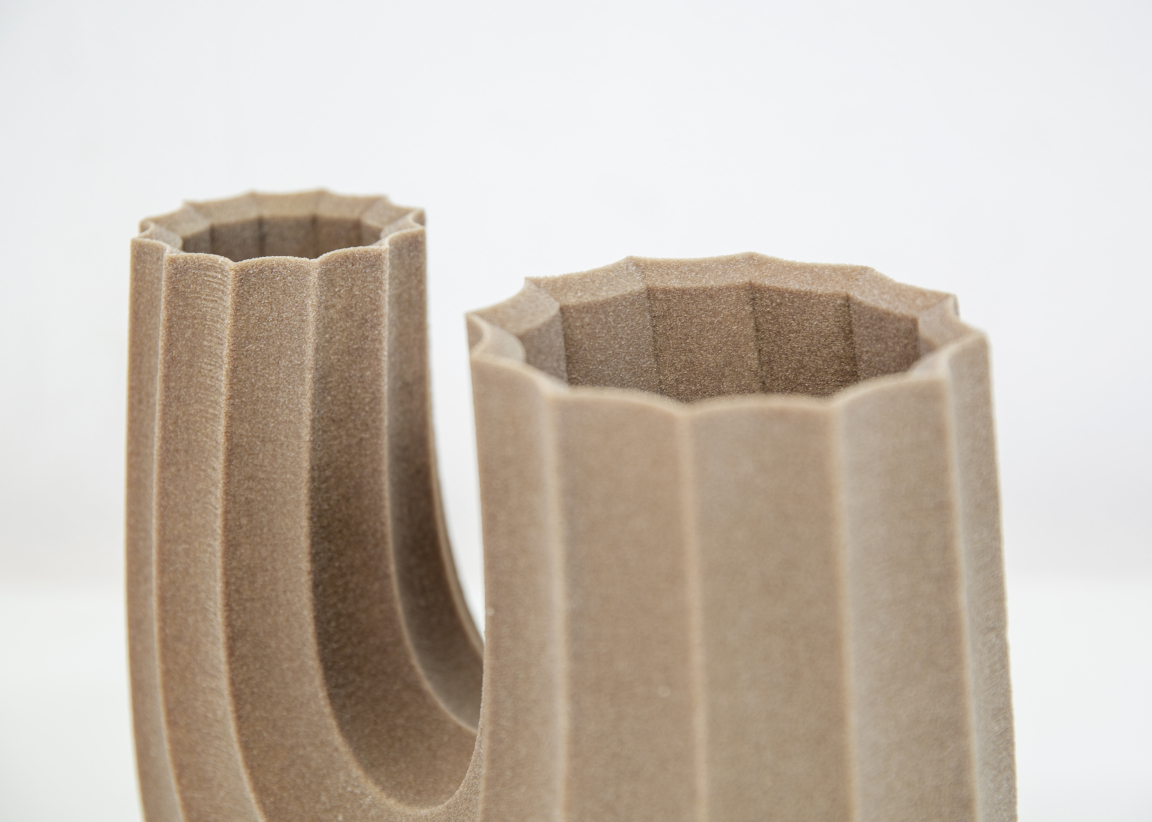
Erco Lai & Sandhelden: Tafoni.
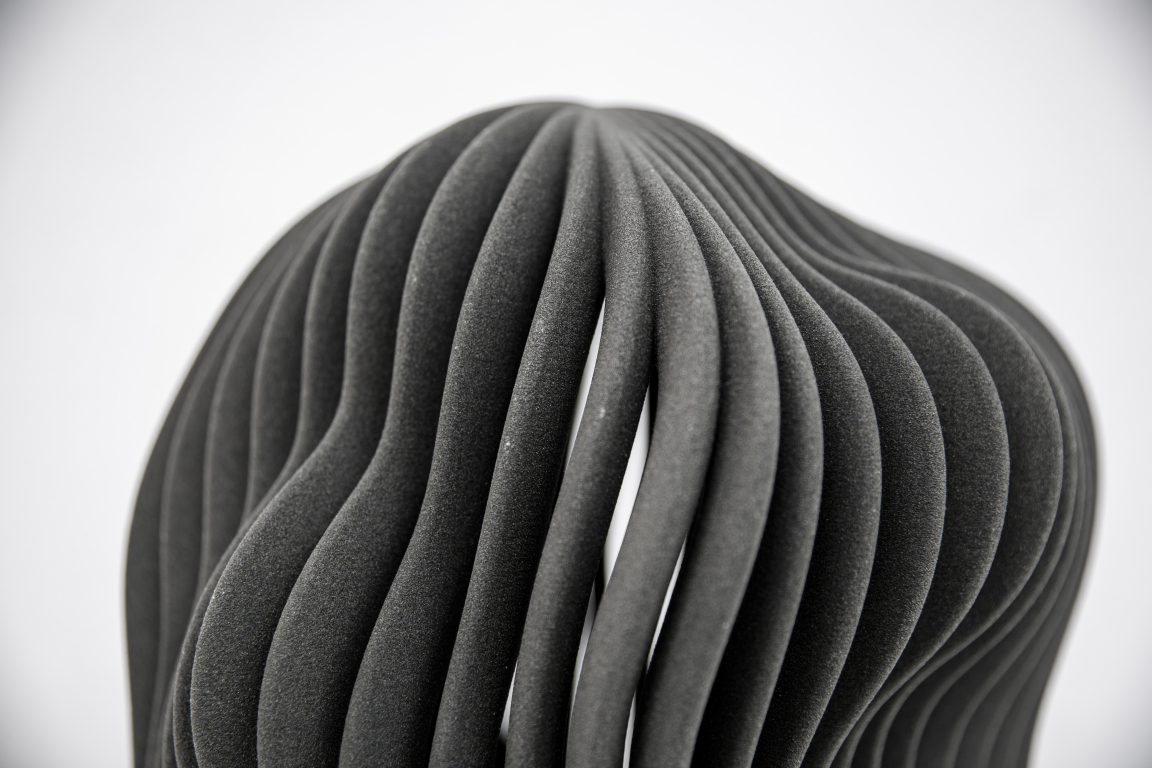
Erco Lai & Sandhelden: Tafoni.
Surface
Digitally derived surfaces are developing dramatically, with biomorphic, fluid forms flowing from the printer nozzle with ease. Using a variety of different softwares, the tactility of hand-crafts such as knit and weave can be produced digitally with an enormous sense of realism, flexibility and delicacy.
18. Wobbly Digital - Playful organic with a tech twist
Wobbly Digital is the creative practice of Soorin Shin – a Glasgow based visual artist & designer, working in 3D printing, new media and installation art. Fusing organic form with a contemporary tech twist, Wobbly Digital takes inspiration from surface qualities inherent of the natural world, such as intertwining roots, spiky horns and smooth pebbles.
Opposing the cold and sharp edged-digital stereotype, Soorin’s works probes at the ambiguous border between the digital and the physical worlds - interrogating the relationship between technology and nature.
Keen to continue to cultivate the innovative emerging artists, designers and craftspeople on our doorstep, Wobbly Digital is our first Maker in Residence in Material Source Studio Glasgow.
Soorin’s practice is also driven by an eco-feminist motivation, which has seen the progressive introduction of more recycled plastic materials into the work. Through her practice, Soorin seeks to encourage the creative field to become a more environmentally conscious space, one 3D printed product or artwork at a time.
You can get up close and see Soorin’s work in the flesh at our Glasgow Studio.
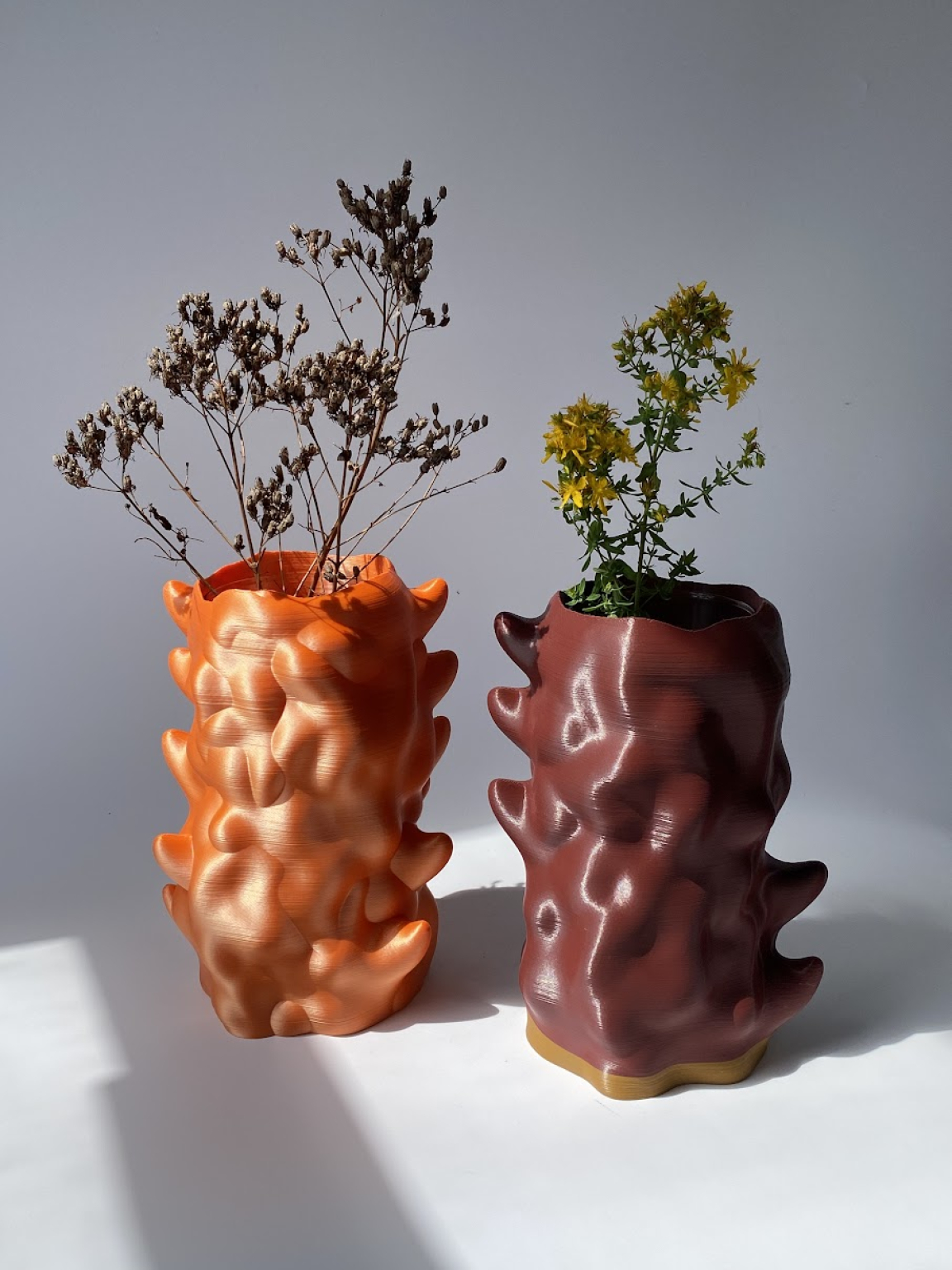
Wobbly Digital: Double Bbul vase.
19. Mark Beecroft – Digital Interlooping
Approaching 3D printing with both tactility and the delicacy of hand-craft at the forefront of their digital design thinking is Manchester-based researcher and designer, Mark Beecroft. Mark completed his BA in Embroidery at the Manchester School of Art, followed by an MA in Textiles.
Through his knowledge and understanding of textiles, Mark questions how both digital fabrication and traditional textile techniques such as knitting and weaving – both integral points of study on the Manchester School of Art textiles course – can be unified.
Using FDR technology, Mark fabricates dainty, inter-looping knitted stitches to create flexible, seamless structures.
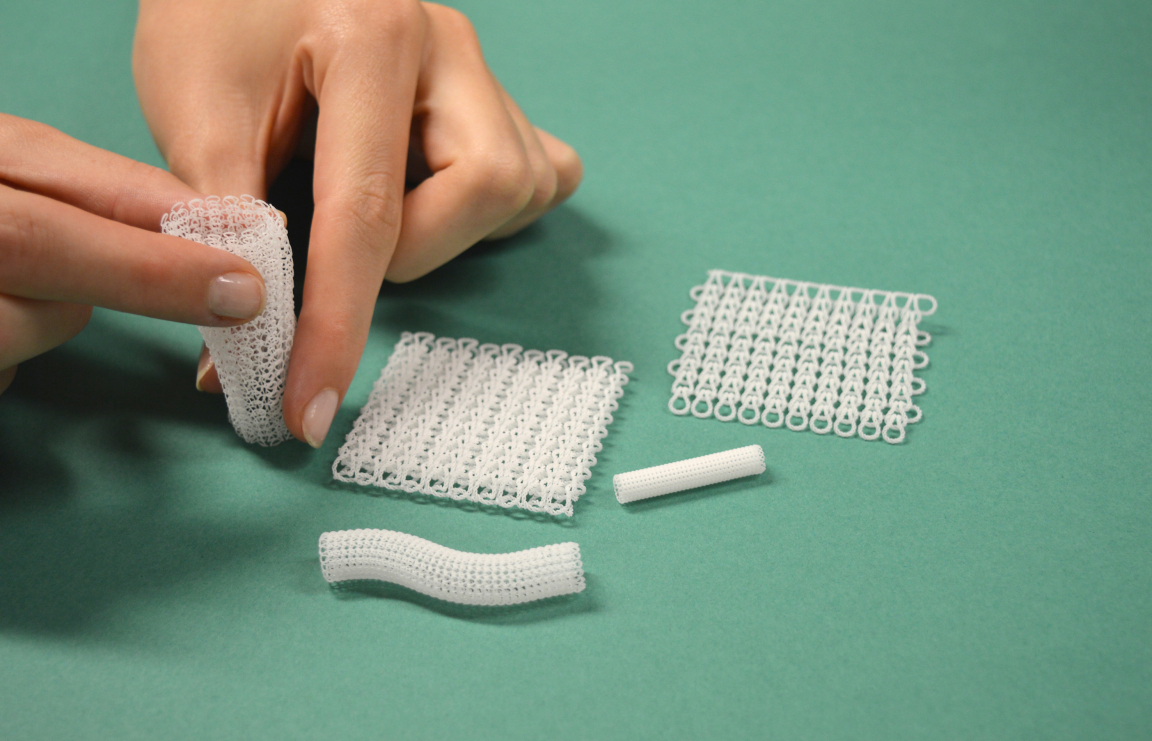
Mark Beecroft: Digital Interlooping.
20. Alex Schofield – Ecological Tectonics
From The Ground Up exhibitor and architectural professor at the California College of the Arts, Alex Schofield is a pioneer of 3D printed biomimetic materials. Operating at the intersection of architecture, fabrication and ecology, Alex endeavors to bring about meaningful solutions to tackle the Climate Crisis.
He has been sharing his 3D printed innovations with the classroom in his building technology seminar, Ecological Tectonics. Co-led by associate professor, Adam Marcs, the seminar focusses on how digital modular ceramic systems can serve as ecological habitats for a variety of species. Building upon existing work at the CCA Architectural Ecologies Lab, robotic equipment is pushed to new creative limits to 3D print ceramic modules that vary in form and texture and in turn, support living systems.
21. Nico Conti – 3D Printing with Porcelain
Fusing tradition with technology, Nico Conti 3D prints vessels in the finest porcelain.
An accomplished digital ceramicist, Nico produces unique 3D printed pieces made from porcelain, with an emphasis on how they interact with light. His work is contemporary and technology driven - likening delicately crafted lace - but draws on a deep understanding of the history and traditions of his craft and materials he uses. Contrary to mass manufacture associated with 3D printing applications, Nico is keen to drive the artistic intention of his works.
Nico splashed onto the ceramic scene, and the cover of the Ceramic Review back in 2021 after being awarded an artist's residency on the strength of his practice at the Ceramics Biennial in Stoke-on-Trent – the Mecca of ceramic craft and production.
Now working from his studio in Malta, Nico continues to push the boundaries of his craft by formulating new recipes for 3D printable porcelains, and building both daring and delicate structures.
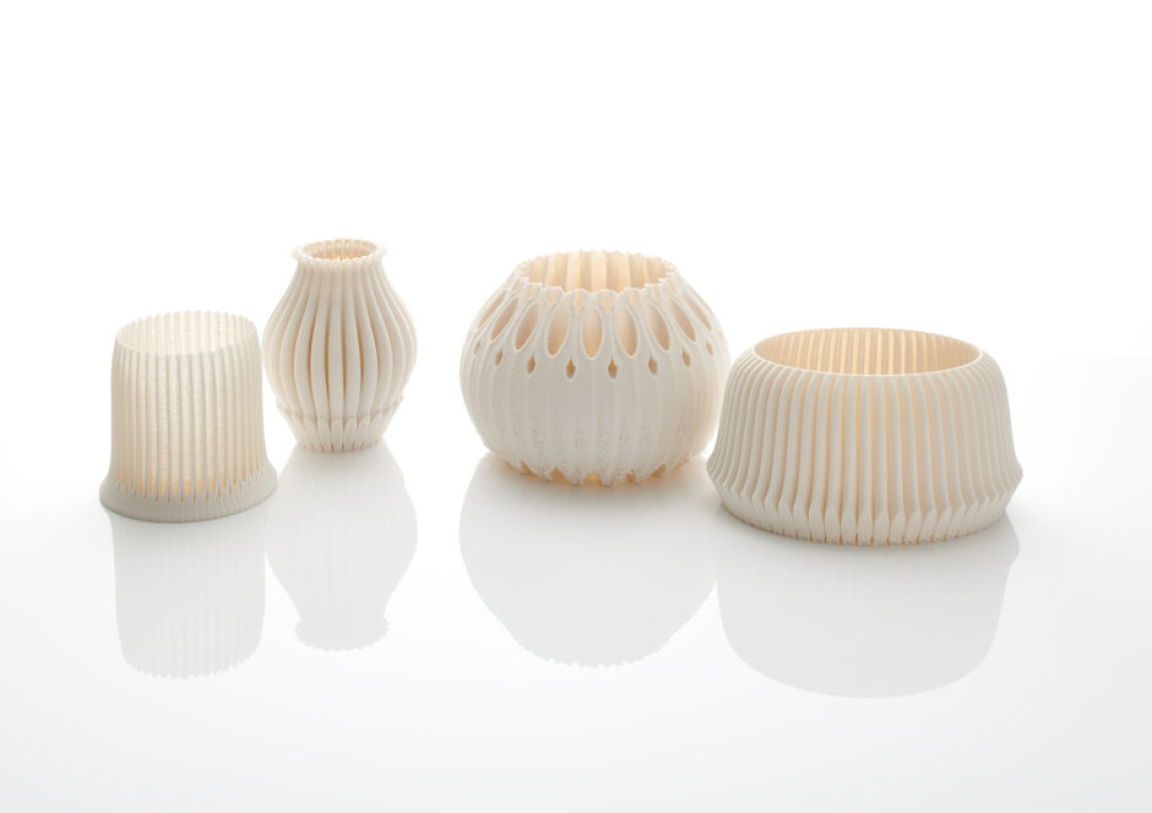
Nico Canti: 3D printed porcelain - credit: Sylvain Deleu
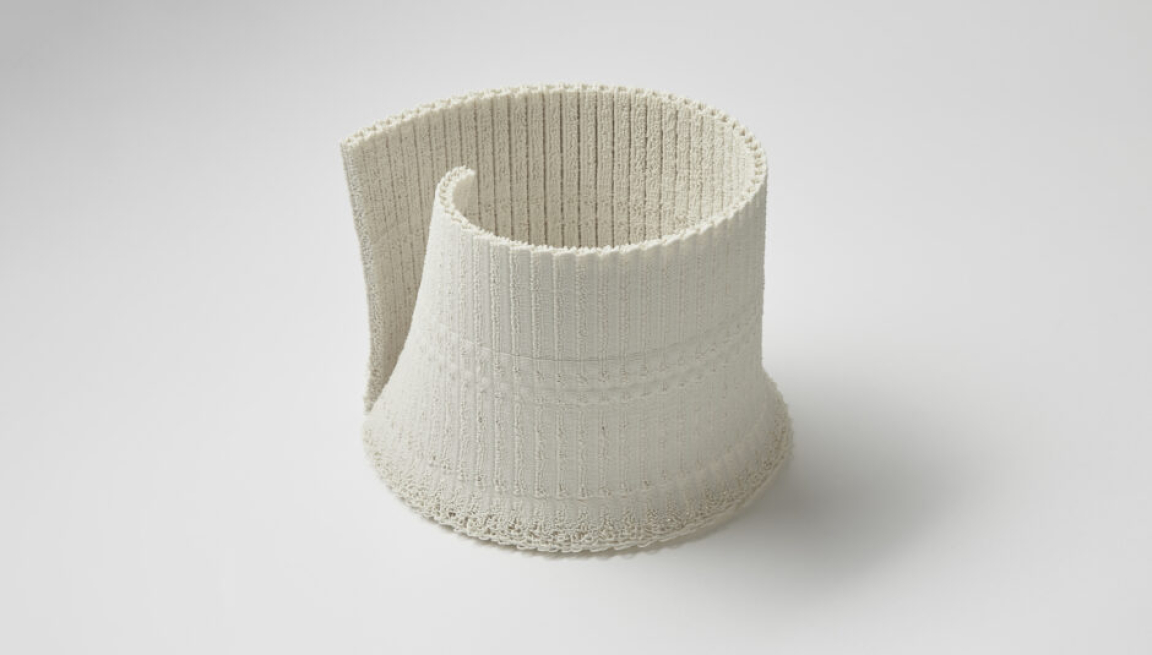
Nico Canti: 3D printed porcelain - credit: Sylvain Deleu
22. ceraLAB – Another Brick in the Wall & Corals
Digital crafting duo, Jan Contala & Philipp Schwaderer are the co-founders of ceraLAB - a 3D printing research and design facility. Between them they explore the applications for robotics within the built environment and the creative sector. With masters degrees in architecture, the Jan and Philipp seek to create intricate 3D printed forms without compromising materiality, sustainability and digital design.
Focusing on ceramics, ceraLAB presents a seamless interaction between nature and machine while pushing the boundaries of craft and digital through sheer curiosity.
ceraLAB’s project, Another Brick in the Wall – is a fresh concept for a 3D printed brick. One of the most used building materials on the planet, it presents the brick of the future as modular and able to serve a wide variety of uses and requirements within a circular economy. ‘Another Brick in the Wall’ showcases the abilities of 3D printing to transform architectural components as we know them.
‘Corals’ is series of 3D printed tables, their form determined by a digitally growing algorithm. In each and every project ceraLAB embarks on, a seamless interaction between natural material and machine is achieved.
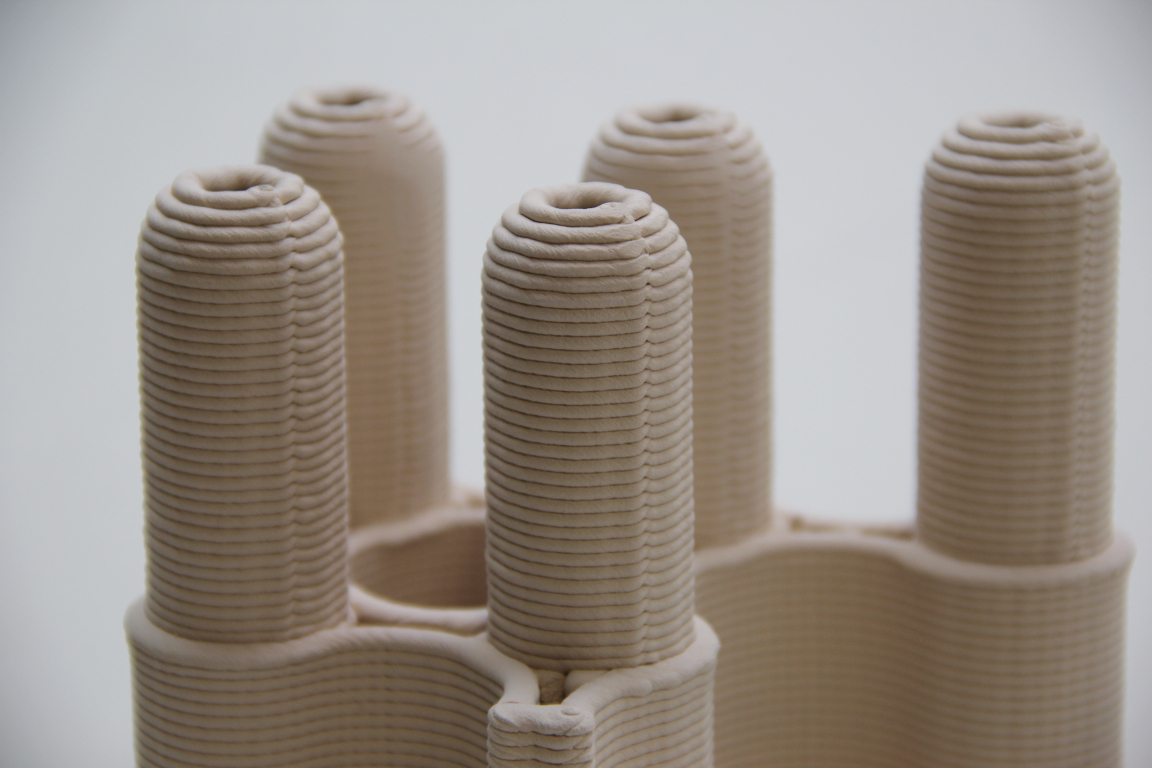
ceraLAB: Another Brick in the Wall.
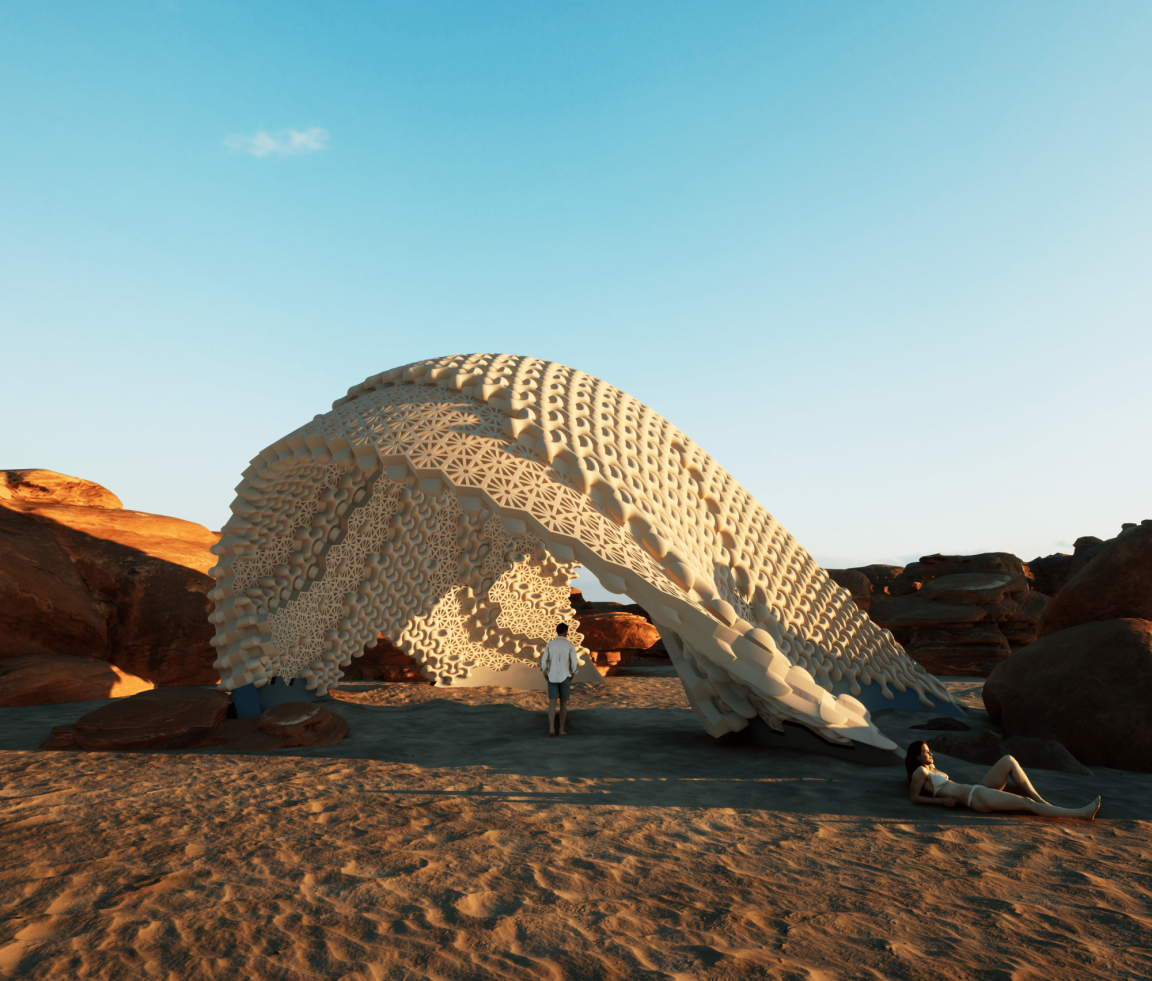
ceraLAB: Another Brick in the Wall.
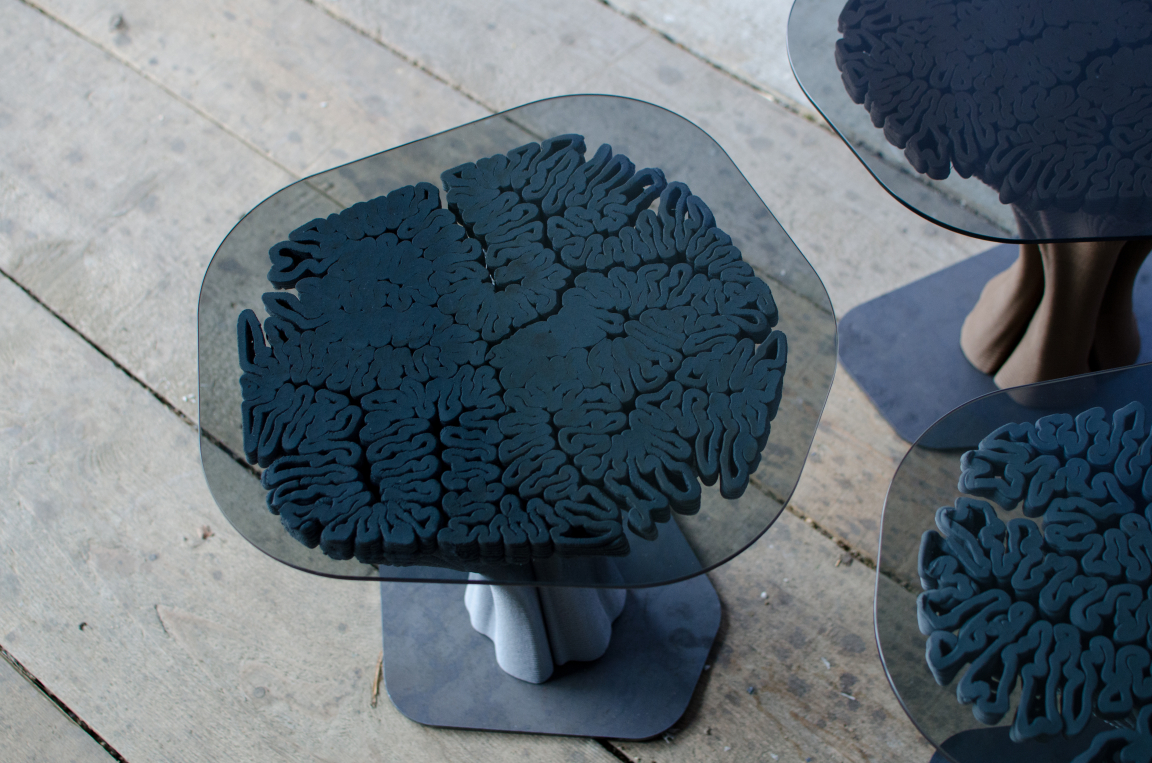
ceraLAB: Corals.
23. Juliette Bekkering and Cristina Nan - 3D printing on sand formwork
Concrete is certainly a problematic material in terms of its sustainability within the construction industry, due to the copious amount of energy, material and water involved in its manufacture. However, can we improve its environmental credentials if we begin to use it differently?
This is the question Juliette Bekkering, Christina Nan and a further team of designers, architects, robotic experts and scientists at Eindhoven University of Technology are investigating.
Spotted at last year’s Dutch Design Week as part of the ‘Drivers for Change Expo’, Juliette Bekkering and Christina Nan presented concrete 3D printing done on a spherical, fully circular mold, robotically fabricated out of sand. A six axis robotic arm then prints patterns on top of the sand mold using a continuous line principle - also found in elements of the natural world like coral.
This approach to biomimetics results in visually appealing design elements - almost like decorative lenses - that can be used in the construction of architectural elements such as facades and walls.
Although the process is at the early stages of development with much more fine-tuning to come, the project demonstrates fresh ideas towards how 3D printing can be carried out and innovative surface qualities for the built environment.
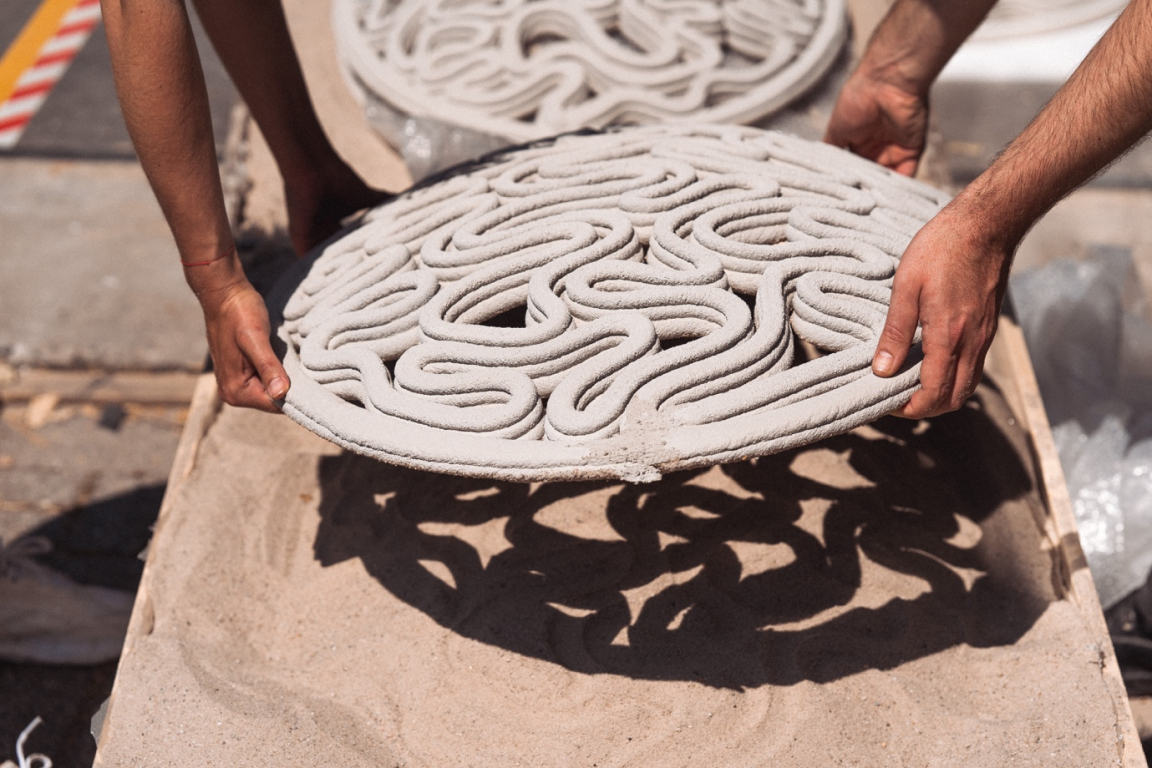
TU Eindhoven, Prof Juliette Bekkering & Cristina Nan: Filigree Freeform Facades.
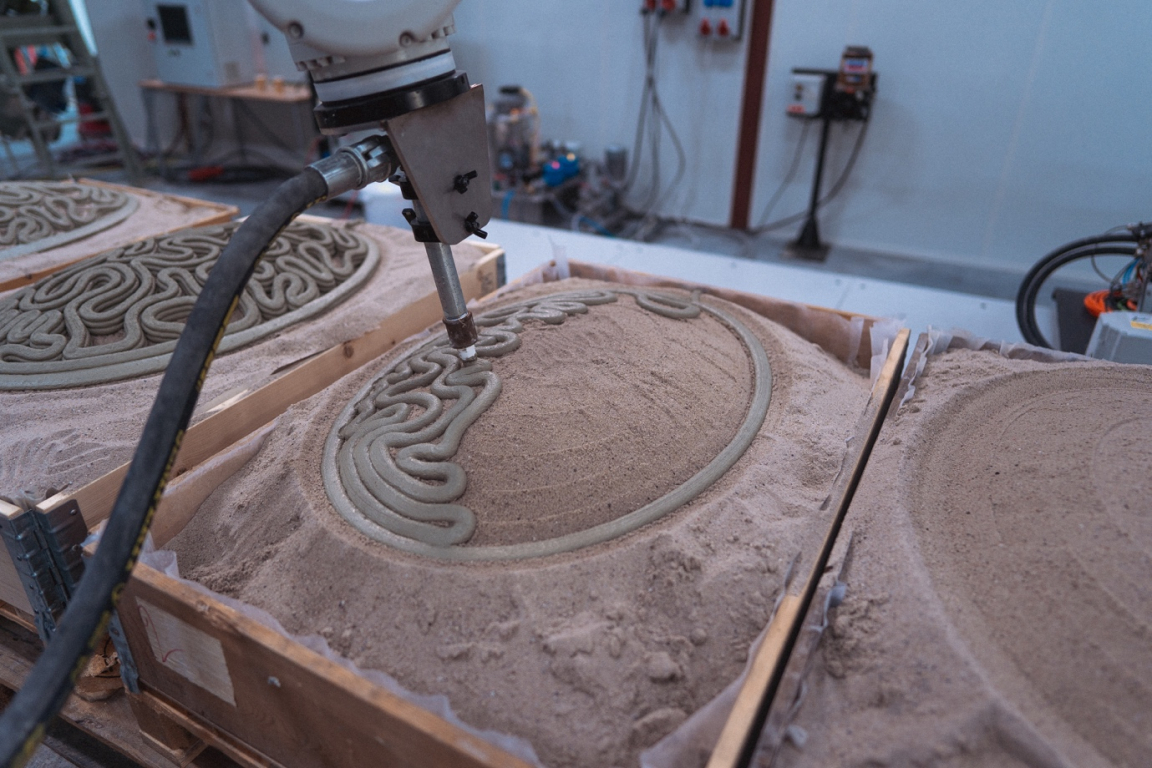
TU Eindhoven, Prof Juliette Bekkering & Cristina Nan: Filigree Freeform Facades.
24. Polymorf - Twisted Columns & The Tectonics of Ornament
Also twisting tradition on architectural materials and structures is Polymorf – an inter-disciplinary research and design practice based in Sweden. Using complex, nature inspired algorithms and innovative 3D printing, Polymorf produces ceramic casts of its renderings, that balance a potter’s craft with cutting-edge technology. Its focus lies in marrying highly organic, nature derived surfaces and forms with applications in architecture and product design.
Twisted Columns is a series of full-scale architectural structures made from mortared together 3D printed ceramic bricks, whilst The Tectonics of Ornament is a project that takes this investigation further. Through rigorous experimentation it explores how its 3D printed bricks can be applied to more conventional and standardised brick-based building systems, such as building for corners, as well as in and around windows and entrances.
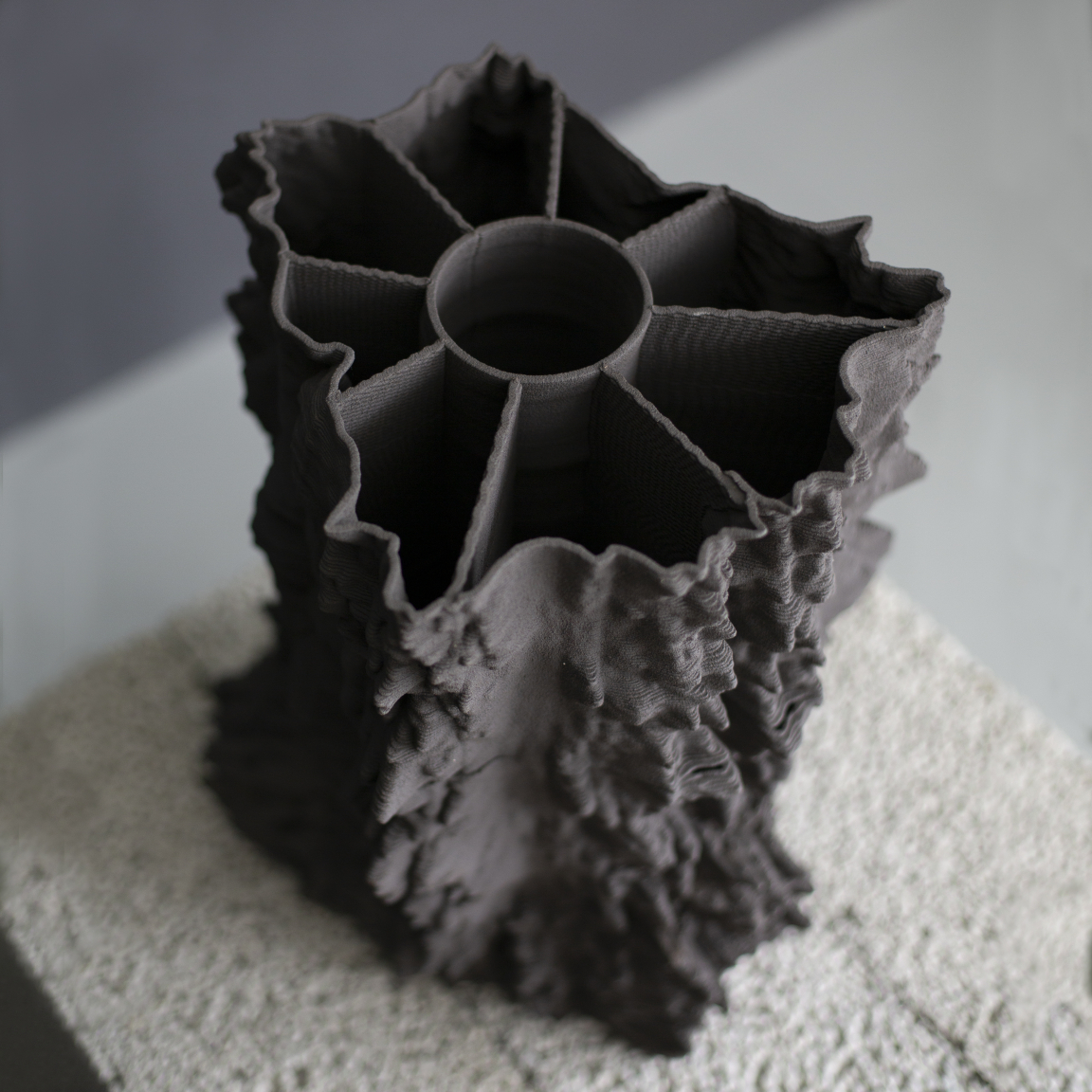
Polymorf: The Tectonics of Ornament.
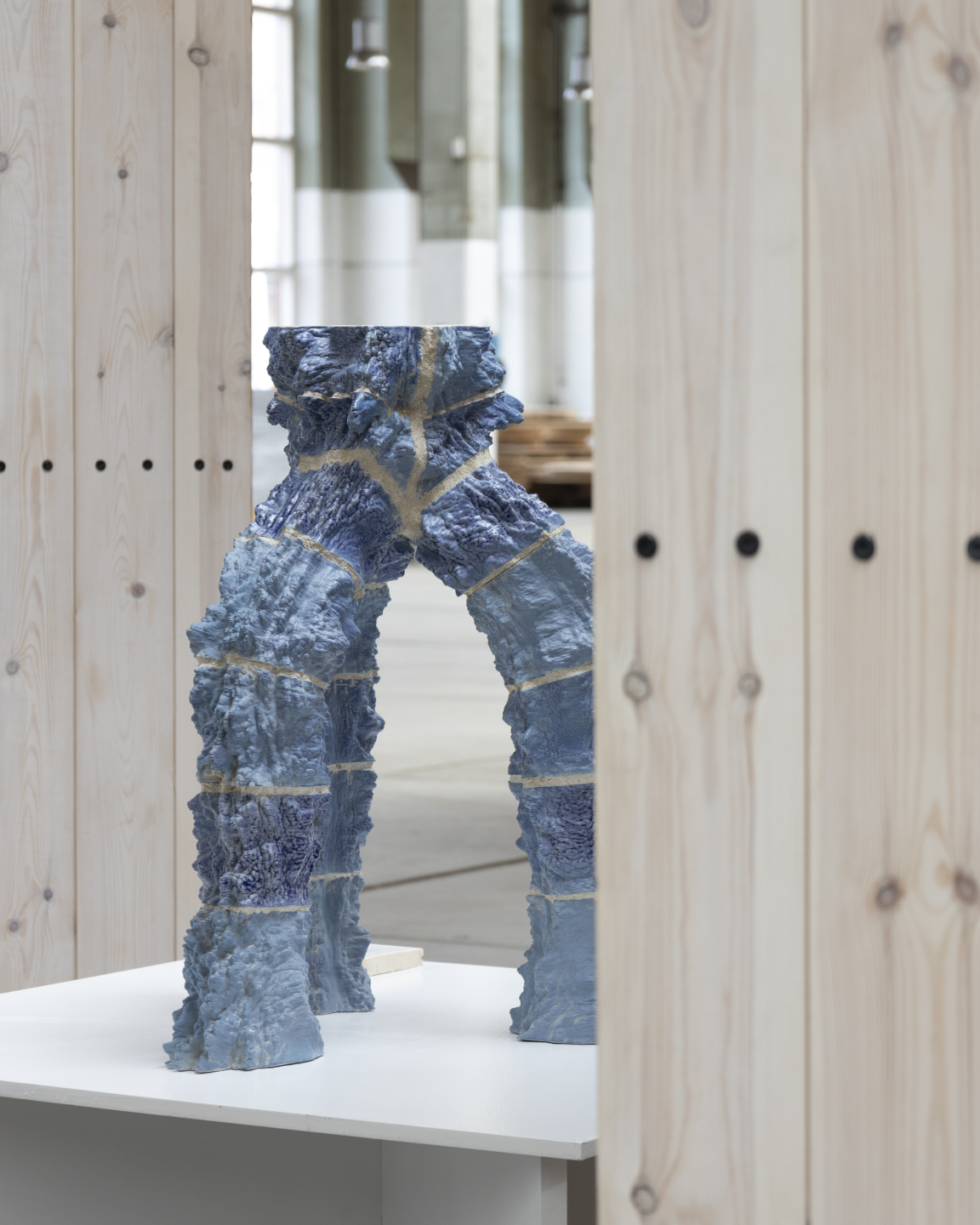
Polymorf: Woven Structures.
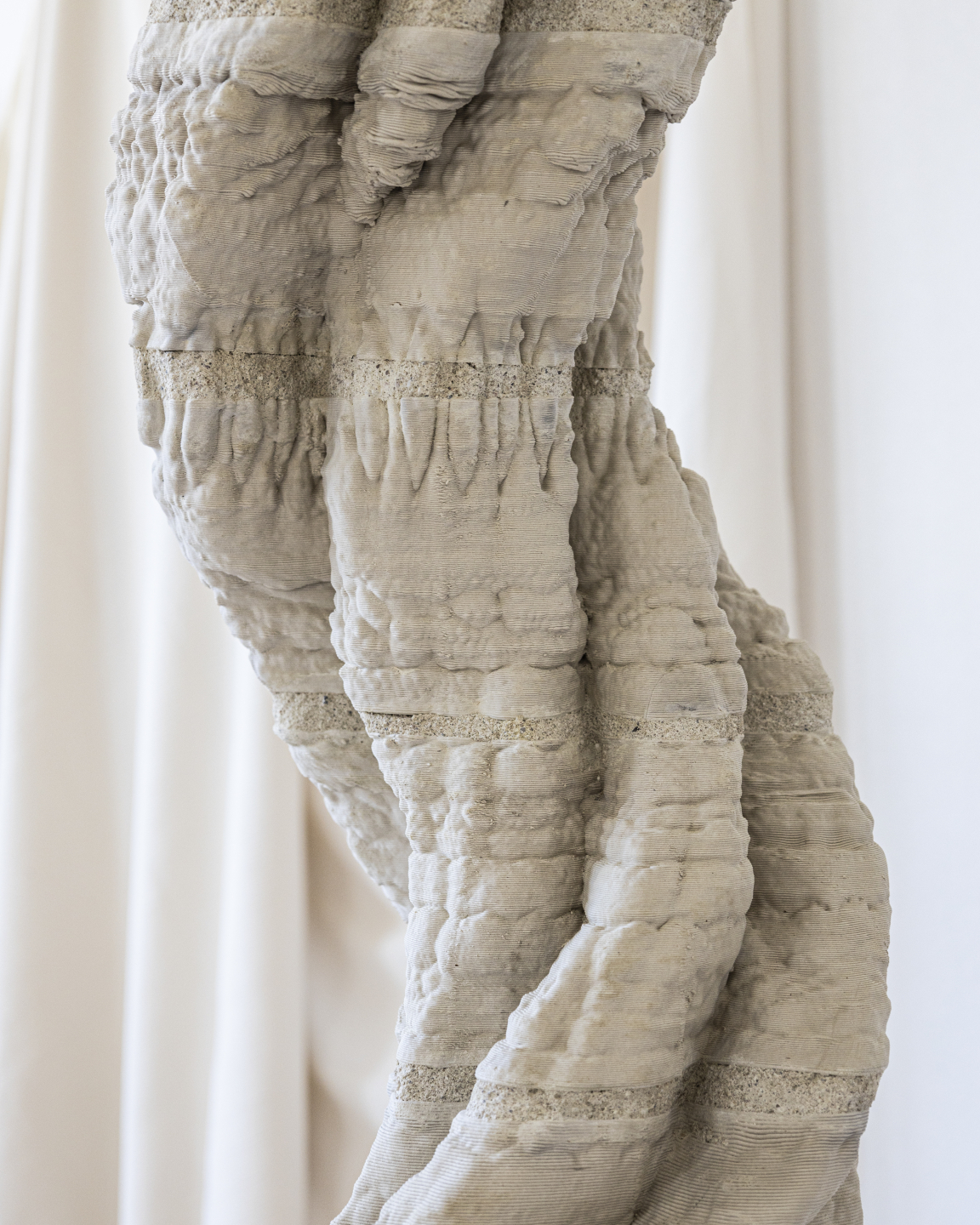
Polymorf: Twisted Column.
Do you have a project to add? Let us know!