With sustainability high on the agenda for designers, it was only a matter of time before a seamless alternative to wood was created.
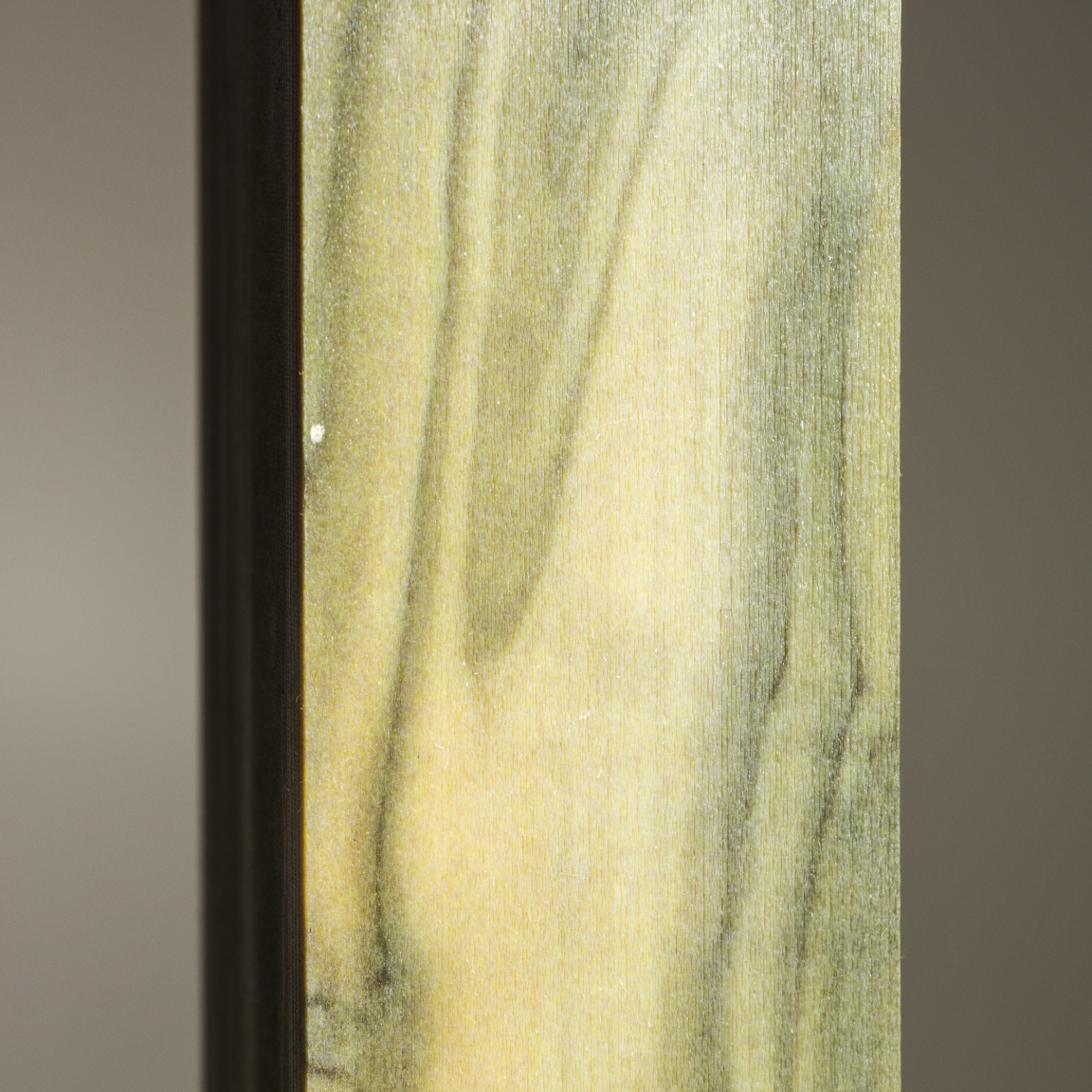
Images by Joni Mici/Columbia Engineering & Jonathan Blutinger/Columbia Engineering
With sustainability high on the agenda for designers, it was only a matter of time before a seamless alternative to wood was created. And now, the wait is over.
Researchers at Columbia University New York have used a “voxel” technique to 3D print a piece of “digital wood”. This has allowed for the same textures found in nature to be seamlessly imitated, right through the entire material composition.
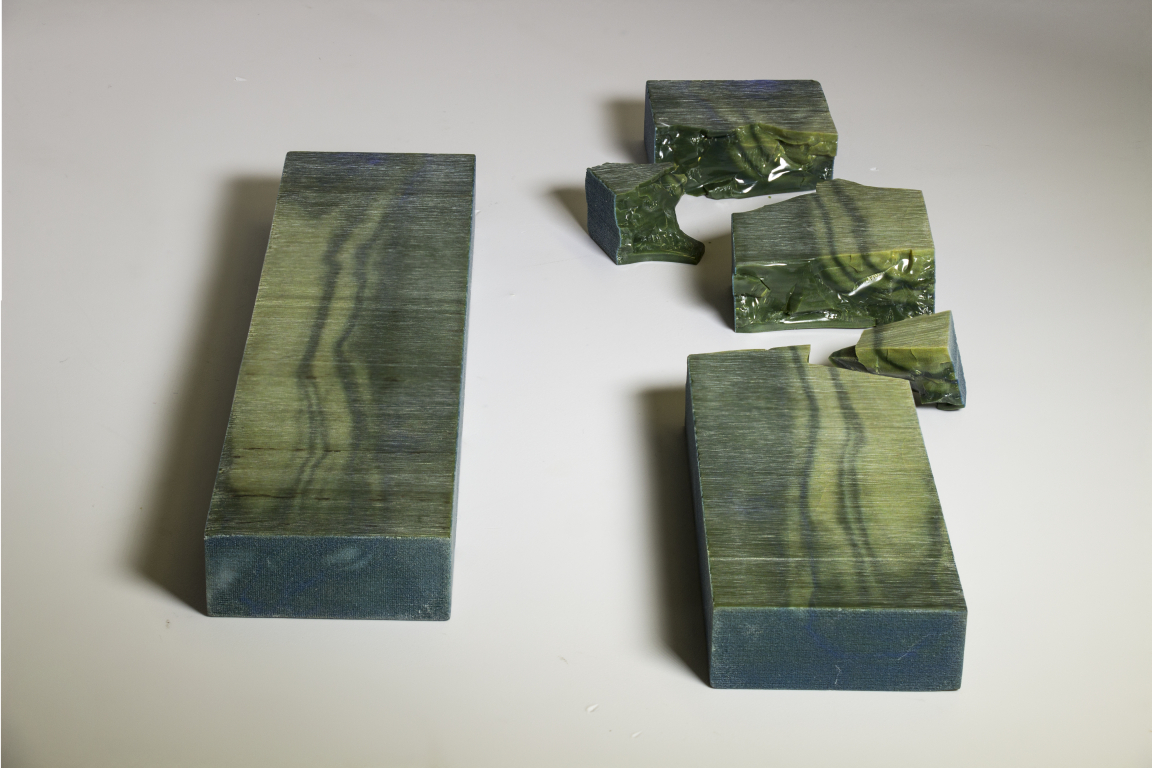
Images by Joni Mici/Columbia Engineering & Jonathan Blutinger/Columbia Engineering
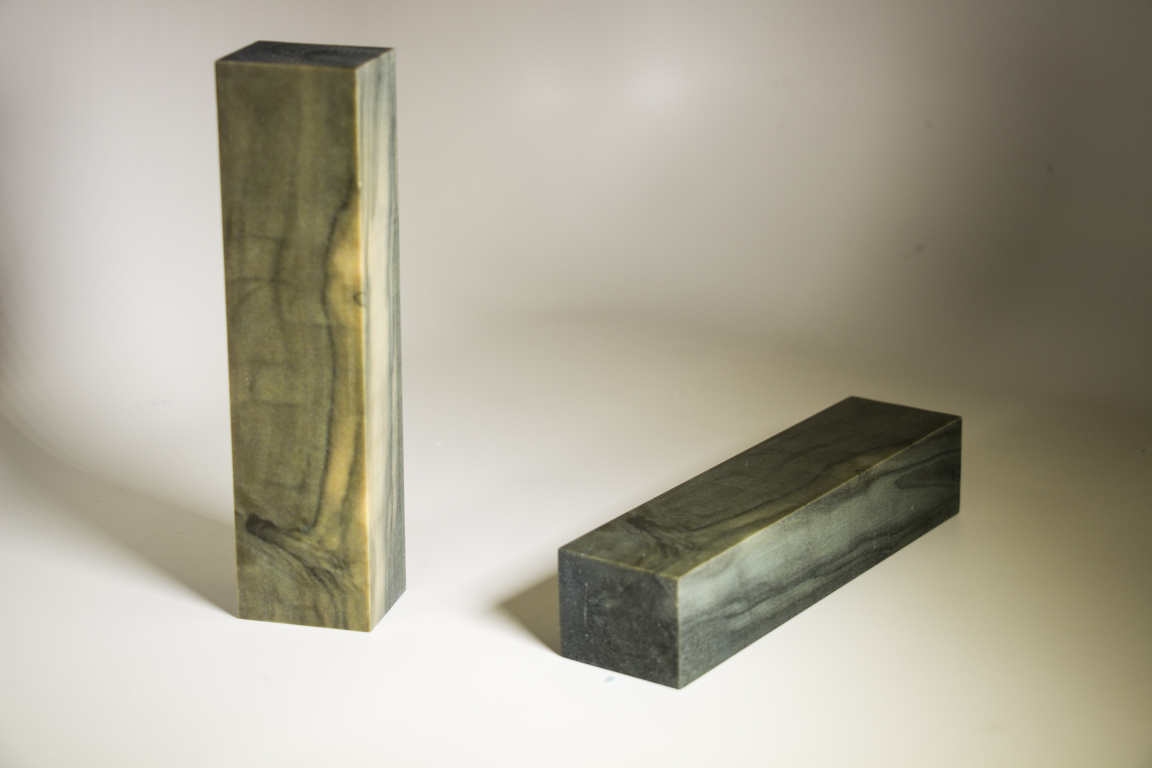
Images by Joni Mici/Columbia Engineering & Jonathan Blutinger/Columbia Engineering
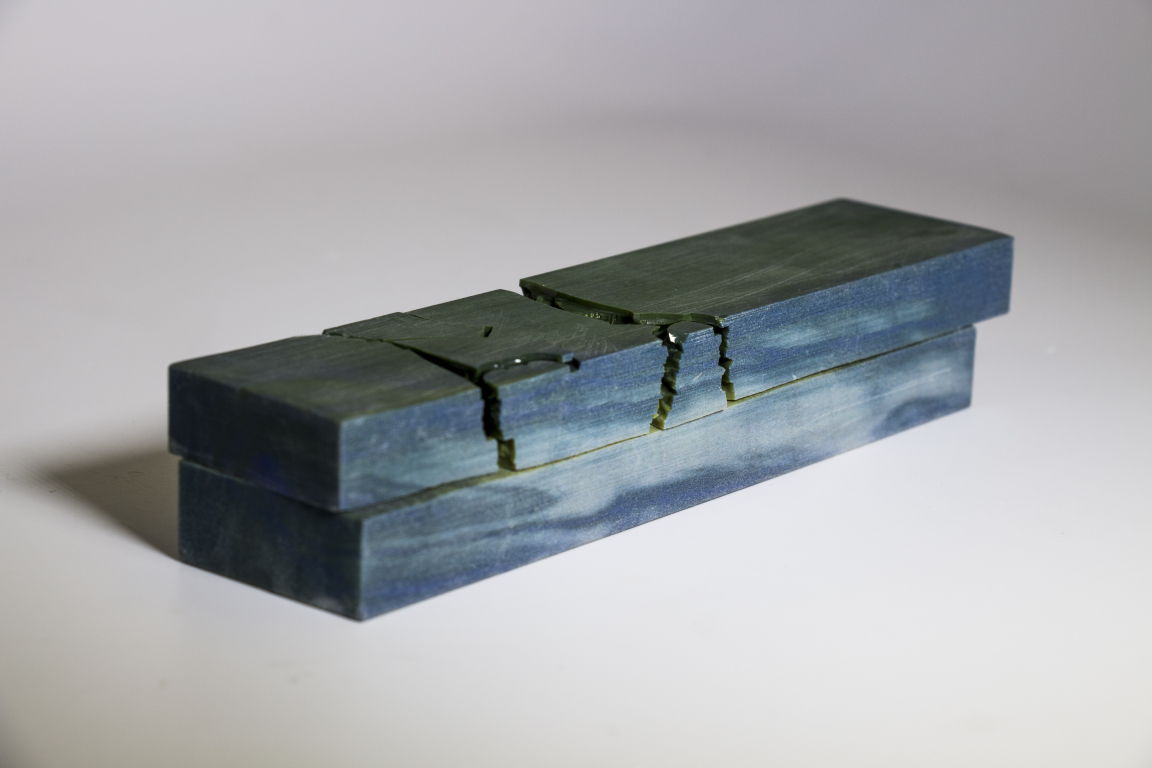
Images by Joni Mici/Columbia Engineering & Jonathan Blutinger/Columbia Engineering
When broken, the internal make-up appears exactly the same as a natural alternative – something that’s never been achieved before.
The innovation was detailed in the report: “Digital Wood: 3D Internal Color Texture Mapping”, where ‘voxel mapping’ is said to have led to the 3D replication of the wood’s texture – olive wood, to be precise.
Voxels are the equivalent of pixels in the 3D process, and are the smallest elements into which an object can be divided.
The creative process involved the use of a destructive imaging technique, which sliced the wood specimen into 27 micrometre pieces on a computer numerical control mill. This resulted in 230 stacked images, which were translated into code for a 3D polyjet printer.
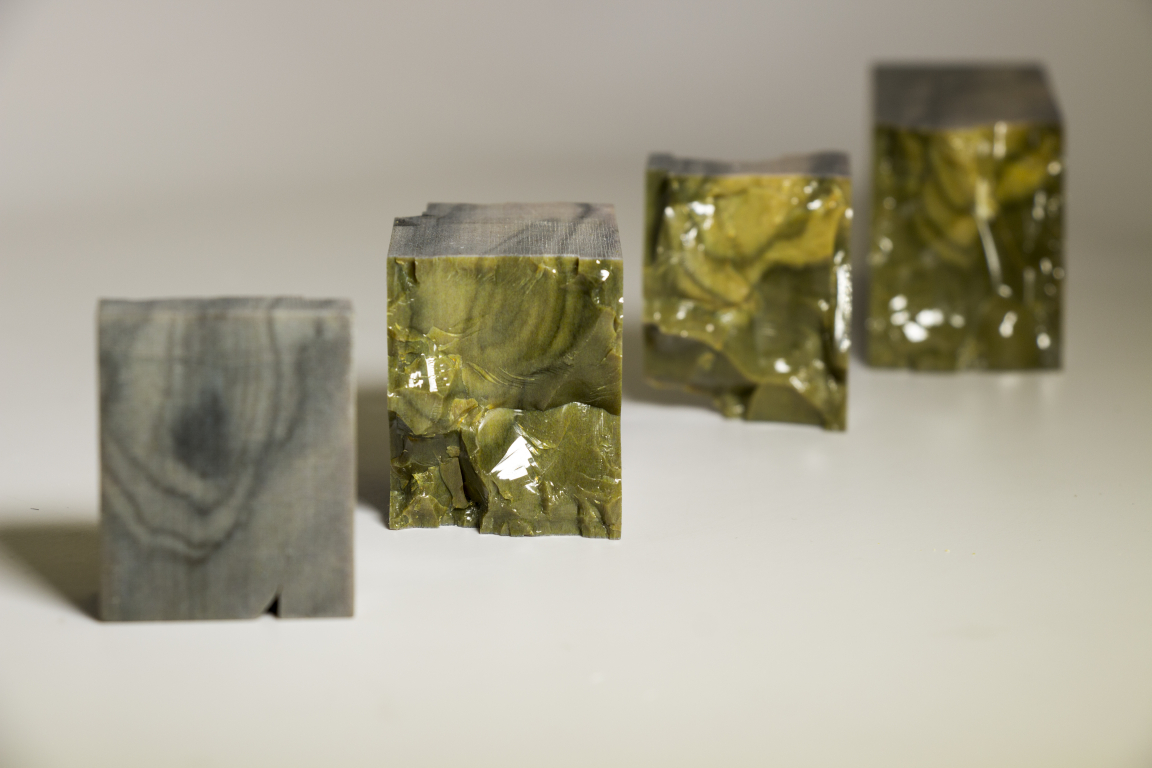
Images by Joni Mici/Columbia Engineering & Jonathan Blutinger/Columbia Engineering
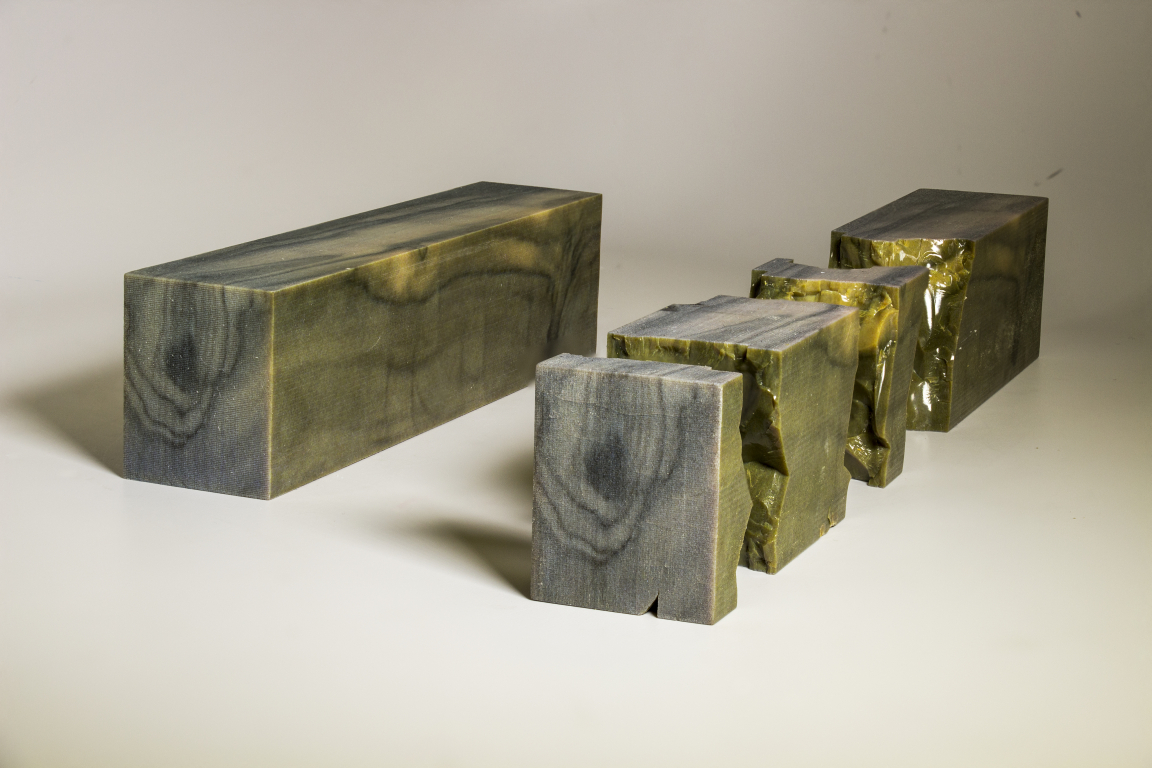
Images by Joni Mici/Columbia Engineering & Jonathan Blutinger/Columbia Engineering
Columbia University’s research team comprised Fabian Stute, Joni Mici, Lewis Chamberlain and Hod Lipson. Of the project, they commented: “Multicolor three-dimensional (3D) printing is typically used for external color textures wrapped around a monomaterial core.
“Here, we present a digital manufacturing workflow comprising destructive tomographic imaging and voxel printing, to replicate both the surface color texture and the internal color texture of anisotropic organic materials such as wood.”
“The final printed object closely resembles the original wooden block both in its external appearance and in its internal color pattern, as confirmed when the block is cut or broken.
“The presented workflow can be employed in digital replication of objects with complex internal patterns that have thus far been impossible to manufacture.”